- Digitaler Zwilling: Aufbau eines Demonstrators für ein fräsendes CPPS
- Der Demonstrator zeigt das Zusammenspiel von Datenerfassung aus Maschine und Prozess, Datenmanagement und Simulationsmodellen.
- Finanzierung durch TRINITY: Digital Technologies, Advanced Robotics and increased Cyber-Security for Agile Production in Future European Manufacturing Ecosystems
- Partner sind TOS Varnsdorf, A.S. und die Technische Universität Dresden
Dresden / Varnsdorf, 15. Februar 2022 – Die Symate GmbH, Hersteller des Softwaresystems Detact für Industrial IoT, Big Data und den Einsatz von Künstlicher Intelligenz (KI) in der Produktion, unterstützt das ‚Trinity‘-Forschungsprojekt an der TU Dresden. In diesem analysiert das Institut für mechatronischen Maschinenbau industrielle Fräsprozesse, um sie für Anwender in einem speziellen Demonstrator nachvollziehbar darzustellen. Hierbei entwickelt Symate mit der Software Detact® spezielle KI-Funktionen für Fräsprozesse.
Das übergeordnete Ziel des Projektes ist eine neuartige Form der nachhaltigen Prozessoptimierung, denn aufgrund der steigenden Anforderungen an Qualität und Produktivität stoßen klassische Methoden zunehmend an ihre Grenzen. Dafür setzen die Forscher auf eine lückenlose Datenerfassung und ein transparentes Simulationsmodell mit einem Digitalen Zwilling, der unmittelbar mit Detact interagiert.
Im Rahmen des Trinity-Projektes wird das Forscherteam ein cyberphysisches Produktionssystem (CPPS) aufbauen, das große Datenmengen (Big Data) in Echtzeit verarbeitet sowie ein reibungsloses Zusammenspiel von Datenerfassung und Simulation garantiert. Diese zentrale Aufgabe übernimmt das Softwaresystem von Symate. Detact wird dafür mit speziellen KI-Funktionen ausgestattet, die in der Lage sind, die entsprechenden Fräsprozesse optimal abzubilden. Zudem erhält das Hardware-Modul ‚Detact Connect‘ einen maßgeschneiderten und hoch leistungsfähigen Schnittstellentreiber.
Hintergrund
Im Bereich der spanenden Fertigung steigen die Anforderungen an Qualität und Produktivität ständig. Diese können mit klassischen Methoden der Prozessverbesserung kaum effizient erfüllt werden. Die Ergebnisse aktueller Forschungsprojekte (TUD) zeigen Möglichkeiten auf, wie Prozessoptimierung mit Hilfe von Prozessdaten in Zusammenarbeit mit Simulationsmodellen funktionieren kann. Für eine industrielle Umsetzung ist jedoch ein reibungsloses Zusammenspiel von Datenerfassung aus Maschine und Prozess, Datenmanagement und Simulationsmodellen notwendig.
In zwei bis drei Jahren werden CPPS-basierte Fertigungsmethoden in der industriellen Bearbeitung eingesetzt, doch im Moment werden sie noch erforscht. Um die erfolgreiche Umsetzung in die Praxis zu ermöglichen, entwickelt Symate mit Detact im Rahmen des Trinity-Projekts spezielle KI-Funktionen für Fräsprozesse. Der POC bietet realistische Testbedingungen für industrielle Big Data Entwicklungen. Zudem möchte der Partner TOS den Demonstrator nutzen, um die Möglichkeiten der CPPS-Technologie kennenzulernen und anhand objektiver Daten zu verstehen, wie die eigenen Entwicklungen angepasst werden müssen. Andererseits möchte TOS mit seinen Kunden eine neue Generation von Maschinen definieren. Zu diesem Zweck soll der Demonstrator in die Produktion eines Fräskopfes überführt werden.
Herausforderungen
Eine wichtige Herausforderung bei der Umsetzung des Demonstrators ist die Echtzeitverarbeitung von Big Data durch leistungsfähige Schnittstellentreiber im Modul Detact Connect, gefolgt von der Umwandlung von Zeit- und Prozessdaten in die geometrische Referenz des Fräsfortschritts am Werkstück. Nicht zuletzt ist die Integration von Fräsprozess-Simulationsmodellen in die Prozesssteuerung anspruchsvoll. Diese Aufgabe wird die IoT-Plattform Detact lösen.
Lösungsweg
Um innovativen Teillösungen in einen CPPS-Demonstrator zu integrieren, übernimmt die IoT-Plattform Detact diese zentralen Aufgaben:
1. Anbindung der ‚Fräsmaschine‘ zur Generierung von Maschinendaten
2. Einsatz von Schnittstellen zur Maschinensteuerung bzw. für die Erfassung der Fräsdaten
3. Integration von APPs zur Analytik und Visualisierung und mit den Schnittstellen zu ‚Milling Digital Twin‘ zur Auswertung des Fräsprozesses und zur simulationsbasierten Vorhersage
4. Erstellen des speziellen Moduls ‚AI-based Control‘
Während die TUD die Arbeiten an der Fräsmaschine (Installation, Tests, Simulationsmodell) durchführt, übernimmt Symate die Entwicklungen auf der IOT-Plattform. TOS liefert zudem die Übertragung des Testaufbaus auf eine Maschine mit Produktionshintergrund. Gleichzeitig ermöglichen die Meilensteine ‚Anbindung des Simulationsmoduls zur Anwendung digitaler Prozessdatenzwillinge‘, ‚Fräsmonitor‘ und ‚Demonstration und Technologietransfer‘ eine solide Projektumsetzung.
Ergebnisse
Im Ergebnis des Projekts entsteht ein Demonstrator für das Frässimulationsmodell, der die Qualität des gefrästen Teils vorhersagen kann. Gleichzeitig berechnet und visualisiert das Bearbeitungssimulationsmodell die Prozessgrößen ortsdiskret. Somit wird es erstmals möglich sein, Live-Daten im Simulationsmodell zu verarbeiten und so einen aktiven digitalen Zwilling aufzubauen.
Nicht zuletzt wird die IOT-Plattform Detact als Integrationsplattform für Echtzeitanwendungen mit umfangreichen Algorithmen zur Datenanalyse und KI etabliert. Mit den Fähigkeiten dieses Systems können Anwender wertvolles Technologiewissen für das Fräsen berechnen.
Disclaimer
Der ‚Demonstrator für das CPPS-Fräsen‘ ist Teil eines Teilprojekts, das indirekt durch das Forschungs- und Innovationsprogramm Horizont 2020 der Europäischen Union über einen offenen Aufruf im Rahmen des Projekts TRINITY (GA Nr. 825196) gefördert wurde.
Über die Symate GmbH
Die Symate GmbH ist ein Spezialist für Künstliche Intelligenz (KI) und Big Data sowie Hersteller des KI-Systems Detact® ‚KI-Infrastruktur & Apps‘. Detact sammelt, analysiert und verarbeitet Produktions- sowie Qualitätsdaten zur systematischen Überwachung und Optimierung von Prozessen. Das neuartige System arbeitet mit nahezu allen Datenquellen bzw. Schnittstellen und nutzt die Methoden der Künstlichen Intelligenz. Es bietet somit flexible Funktionalitäten für eine automatisierte Prozessüberwachung und nachhaltige Prozesstransparenz. Damit übernimmt Detact auch verschiedene Aufgaben eines klassischen MES (Manufacturing Execution System), geht aber weit darüber hinaus. Bei Bedarf kann das Softwaresystem der Symate GmbH sogar an ein bestehendes MES, BDE oder CAQ angebunden werden, um dessen Funktionalitäten gezielt zu erweitern.
Mit Detact erhalten Anwender nicht nur ein detaillierteres Prozessverständnis, sondern auch digitale Assistenten für verschiedenste Szenarien rund um ihren Fertigungsprozess. Die Basis dafür bilden mehr als 15 browser-basierte Apps, die sich für kleine, mittlere und große Anwendungen individuell anpassen lassen. Detact wird von zahlreichen Firmen aus den Bereichen Automobil, Kunststoff, Maschinenbau, Luftfahrt, Leichtbau, Medizintechnik und Additive Fertigung etc. sehr erfolgreich eingesetzt. Weitere Informationen über Detact und die Symate GmbH finden Sie im Internet unter detact.de bzw. unter symate.de
PDF-Version dieser News:
2022-02-15_Symate-Pressemitteilung_Trinity
Bild zur Meldung:
Copyright: TU Dresden, Trinity
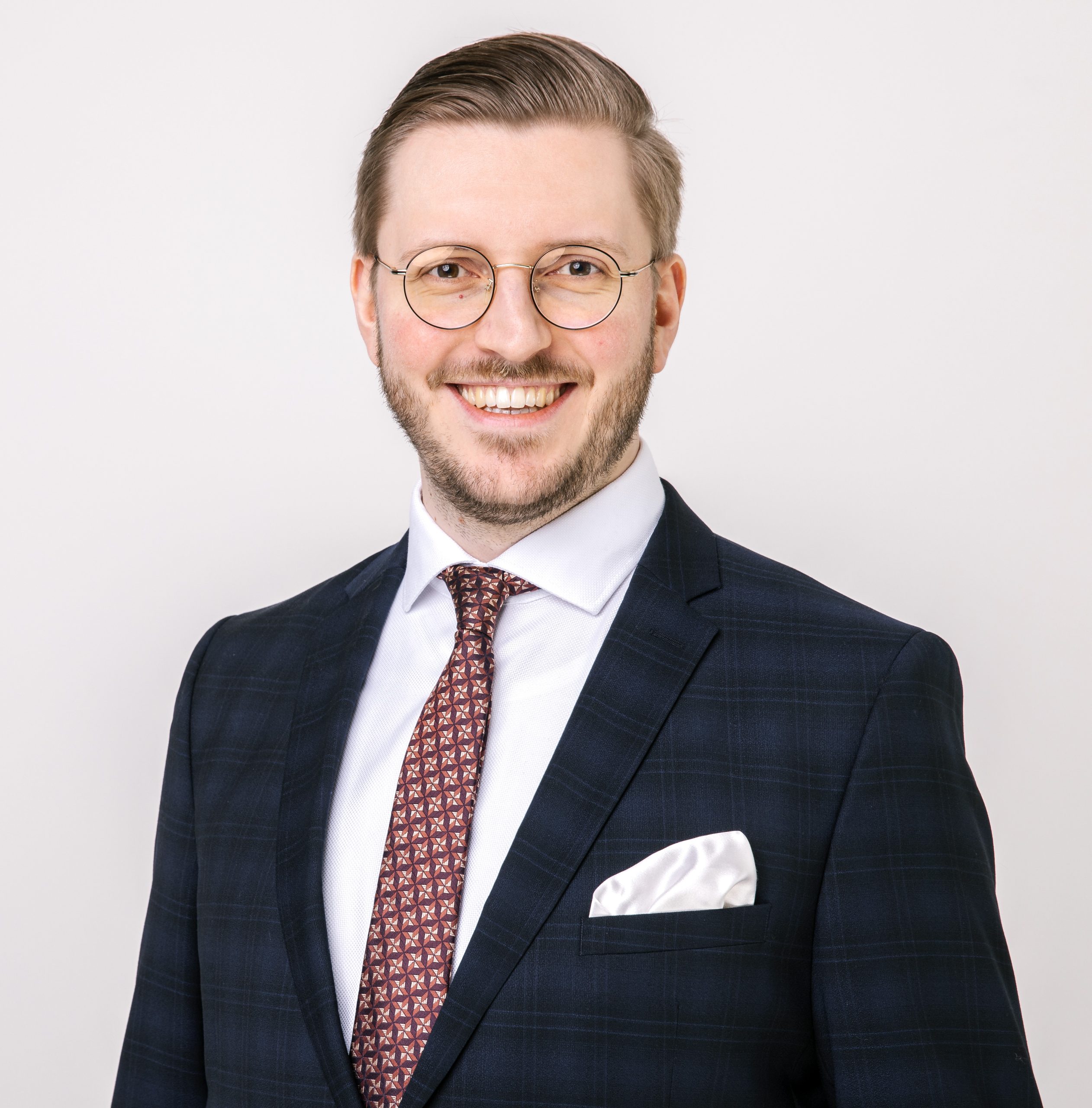
ALEXANDER SCHERER
Das könnte Sie auch interessieren:
So nutzen unsere Kunden Detact!