Big Data für ein Quality Prediction bei der Tape Ablage
Ein Softsensor für die Herstellung von großen Flugzeugteilen
- Fiber-Placement: DLR entwickelt neuartige Technologien und Verfahren für selbstregulierende Leichtbauprozesse
- Industrie 4.0 mit dem Menschen im Fokus: Neuartiger KI-Softsensor unterstützt Prozess- bzw. Qualitätsdatenanalyse des DLR
- Intelligente Datenfusion: Online-Überwachung mit virtuellem Sensor ist rein physikalischen Systemen überlegen
- Assistenzsystem: Entscheidungsprozess in Bezug auf Reparatur und Nacharbeit vereinfacht
Dresden/ Stade, 6. Dezember 2021 – Die Symate GmbH, Spezialist für die Optimierung von Fertigungsprozessen mit den Methoden der Künstlichen Intelligenz (KI), entwickelt einen KI-basierten Softsensor für das Deutsche Zentrum für Luft- und Raumfahrt e.V. (DLR). Die technische Basis für den neuen Softsensor bildet die KI-Software Detact. Mit der Entscheidung für Detact erhält die Dresdner Symate GmbH den Zuschlag in einer deutschlandweiten Ausschreibung des DLR. Die neue Lösung arbeitet mit Daten aus der Qualitätssicherung von Faserverbundablegeprozessen und vereinfacht den Entscheidungsprozess in Bezug auf Reparatur und Nacharbeit bei der Herstellung von Flugzeugstrukturen.
Das DLR wird den Detact-Softsensor an das bestehende MES (Manufacturing Execution System) der sogenannten GroFi®-Anlage am Standort Stade anschließen. Der Softsensor wird hier den Qualitätssicherungsprozess unterstützen.
Mithilfe des neuen Softsensors erforscht das DLR den Multimaterialleichtbau unter industrienahen Bedingungen. Im Fokus steht die Entwicklung eines automatisierten Faserablageprozesses (engl. Automated Fiber Placement, kurz AFP) für die Herstellung von großflächigen, hochintegralen Multimaterial-Leichtbauteilen. Mittels AFP wird beispielsweise der Bug- und Cockpitbereich des Dreamliner 787 von Boeing hergestellt, ebenso wie Flügel- und Rumpfstrukturen des Airbus A350.
So funktioniert das AFP-Verfahren
In Stade forscht das DLR u.a. im Bereich automatisierte Faserablage zur Herstellung von großskaligen und komplexen Multimaterialleichtbauteilen unter industrienahen Bedingungen. Hier verspricht das Automated Fiber Placement (AFP) eine besonders effiziente Fertigung.
Beim AFP-Verfahren werden spezielle Laminatbänder mit wenigen Millimetern Breite (sog. ‚Tows‘) von Robotern Bahn für Bahn ‚nebeneinander‘ sowie Lage für Lage ‚übereinander‘ gelegt und danach in einem Autoklav verpresst sowie ausgehärtet. Im Verlauf dieser Prozessschritte entsteht so die endgültige Bauteilgeometrie.
Das AFP-Verfahren bietet großartige Möglichkeiten, hat jedoch auch einen kritischen Punkt: Aufgrund der individuellen Form der Bauteile können die einzelnen Tows nicht immer exakt positioniert werden. Bei Bedarf ist bspw. auch eine bogenförmige Anordnung erforderlich. Somit entstehen zwangsläufig Lücken, Überlappungen oder Verdrehungen. Diese und andere mögliche Abweichungen haben einen entscheidenden Einfluss auf die Qualität der Bauteile und können vor allem im Flugzeugbau dramatische Folgen haben. Daher müssen Fertigungsprozesse im AFP-Verfahren sehr genau überwacht und Abweichungen aufwändig korrigiert werden.
Hierzu kommentiert Falk Heinecke, Teil einer Forschergruppe im Bereich automatisierte Faserablage: „Bei der Herstellung von großen Leichtbauteilen bietet das AFP-Verfahren einzigartige Möglichkeiten. Aber Abweichungen beim Verlegen der einzelnen Tows lassen sich nicht vermeiden. Die hohen Qualitätsanforderungen im Luftfahrtbereich erfordern eine genaue Prüfung, häufig manuelle Inspektion und ggf. Nacharbeit sowie Korrektur dieser Abweichungen. Bei der Herstellung eines großen Rumpfsegmentes kann beispielsweise der Zeitaufwand für Inspektion, Reparatur und Nacharbeit nicht-tolerierbarer Abweichungen mehr als 30 Prozent der gesamten Fertigungszeit ausmachen. Genau an dieser Stelle setzt unser Softsensor als Assistenzsystem im Bereich der Qualitätssicherung an. Unser Ziel ist die Einsparung von Kosten durch eine Verringerung von Standzeiten der Maschinen sowie eine Vereinfachung des Entscheidungsprozesses in Bezug auf Reparatur und Nacharbeit. Daher freuen wir uns auf die Zusammenarbeit mit der Symate GmbH. Mit diesem Unternehmen haben wir einen Partner, der das richtige Know-how und die Technologie besitzt, um uns bei der Weiterentwicklung im Bereich der automatisierten Faserablage zu unterstützen. Der Detact-Softsensor, den Symate derzeit für uns entwickelt, wird eine zusätzliche Informationsquelle während unserer Qualitätssicherung bilden. Der neue Softsensor wird unsere Simulationen mit den Daten aus der realen Fertigung in Echtzeit vergleichen. So können wir die Qualität der Bauteile bereits im laufenden Prozess prognostizieren und frühzeitig intervenieren.“
Die Aufgaben des Softsensors
Mit dem neuen Softsensor, der auf dem KI-System Detact basiert, realisiert das DLR ein intelligentes Assistenzsystem im Qualitätssicherungsprozess. Dieses System verknüpft Daten aus Simulationen mit prozessbegleitenden Messungen. Eine Vielzahl von Informationen wird dabei vollautomatisch analysiert. Die KI-Spezialisten von Symate haben bereits damit begonnen, den Softsensor nach den Vorgaben des DLR zu programmieren, damit er mit dem vorhandenen optischen Messsystem und den Simulationsdaten aus der DLR-Datenbank verbunden werden. Sobald alle Vorbereitungen abgeschlossen sind, kann der Sensor als Onlineüberwachungs-Tool an der Forschungsanlage eingesetzt werden und die DLR-spezifischen Zielgrößen aus den vorhandenen Daten in Echtzeit errechnen.
Hierzu erläutert Dr. Martin Juhrisch, Geschäftsführer der Symate GmbH: „Durch seine künstliche Intelligenz wird der Detact-Softsensor das Qualitäts- und Toleranzmanagement des DLR auf ein neues Level heben und eine vollautomatische Inline-Quality-Prediction realisieren. Das DLR wird während der noch laufenden Produktion valide Qualitätsvorhersagen treffen und die Ablegeprozesse in einem vorab definierten Fenster überwachen können. Dabei lernen die Forscher die Grenzen von realistischen Prozessfenstern immer besser kennen und können tolerierbare Abweichungen im System hinterlegen.“
Mithilfe der gewonnenen Daten wird der Softsensor Schritt für Schritt ein eigenes KI-Modell aufbauen, das sowohl interne als auch externe Einflüsse auf die Bauteilqualität enthält.
Heinecke meint abschließend: „Mit dem Detact-Softsensor realisieren wir die Qualitätssicherung bei der automatisierten Faserablage nach dem Vorbild der Industrie 4.0. Allerdings steht der Mensch als Entscheidungsträger weiterhin im Mittelpunkt. Wir werden ihn zunächst einsetzen, um den Entscheidungsprozess in Bezug auf Reparatur und Nacharbeit bei der Herstellung von Flugzeugstrukturen zu vereinfachen. Vergleichbare Lösungen sind später auch für andere Branchen leicht realisierbar.“
Über die Symate GmbH
Die Symate GmbH ist ein Spezialist für Künstliche Intelligenz (KI) und Big Data sowie Hersteller des KI-Systems Detact® ‚KI-Infrastruktur & Apps‘. Detact sammelt, analysiert und verarbeitet Produktions- sowie Qualitätsdaten zur systematischen Überwachung und Optimierung von Prozessen. Das neuartige System arbeitet mit nahezu allen Datenquellen bzw. Schnittstellen und nutzt die Methoden der Künstlichen Intelligenz. Es bietet somit flexible Funktionalitäten für eine automatisierte Prozessüberwachung und nachhaltige Prozesstransparenz. Damit übernimmt Detact verschiedene Aufgaben eines klassischen MES (Manufacturing Execution System), geht aber weit darüber hinaus. Bei Bedarf kann das Softwaresystem der Symate GmbH sogar an ein bestehendes MES, BDE oder CAQ angebunden werden, um dessen Funktionalitäten gezielt zu erweitern.
Mit Detact erhalten Anwender nicht nur ein detaillierteres Prozessverständnis, sondern auch digitale Assistenten für verschiedenste Szenarien rund um ihren Fertigungsprozess. Die Basis dafür bilden mehr als 15 browser-basierte Apps, die sich für kleine, mittlere und große Anwendungen individuell anpassen lassen. Detact wird von zahlreichen Firmen aus den Bereichen Automobil, Kunststoff, Maschinenbau, Luftfahrt, Leichtbau, Medizintechnik und Additive Fertigung etc. sehr erfolgreich eingesetzt. Weitere Informationen über Detact und die Symate GmbH finden Sie im Internet unter detact.de bzw. unter symate.de.
Über das DLR/ Deutsches Zentrum für Luft- und Raumfahrt e.V.
Das DLR ist das Forschungszentrum der Bundesrepublik Deutschland für Luft- und Raumfahrt. Es betreibt Forschung und Entwicklung in Luftfahrt, Raumfahrt, Energie und Verkehr, Sicherheit und Digitalisierung. Die Deutsche Raumfahrtagentur im DLR ist im Auftrag der Bundesregierung für die Planung und Umsetzung der deutschen Raumfahrtaktivitäten zuständig. Zwei DLR Projektträger betreuen Förderprogramme und unterstützen den Wissenstransfer.
Global wandeln sich Klima, Mobilität und Technologie. Das DLR nutzt das Know-how seiner
55 Institute und Einrichtungen, um Lösungen für diese Herausforderungen zu entwickeln. Unsere 10.000 Mitarbeitenden haben eine gemeinsame Mission: Wir erforschen Erde und Weltall und entwickeln Technologien für eine nachhaltige Zukunft. So tragen wir dazu bei, den Wissens- und Wirtschaftsstandort Deutschland zu stärken. Weitere Informationen über das DLR finden Sie im Internet unter www.dlr.de.
Kontakt:
Symate GmbH
David Haferkorn
Produkt Management &
Business Development
Georg-Treu-Platz 3
01067 Dresden
Tel.: +49 (0)351 82126 -300
Fax: +49 (0)351 82126 -399
E-Mail: info@symate.de
Eine PDF-Version dieser Pressemitteilung finden Sie hier:
Copyright:
Deutsches Zentrum für Luft- und Raumfahrt e.V. – DLR
Dieses Bild kann für Presseveröffentlichungen
über Symate und das DLR kostenfrei
verwendet werden.
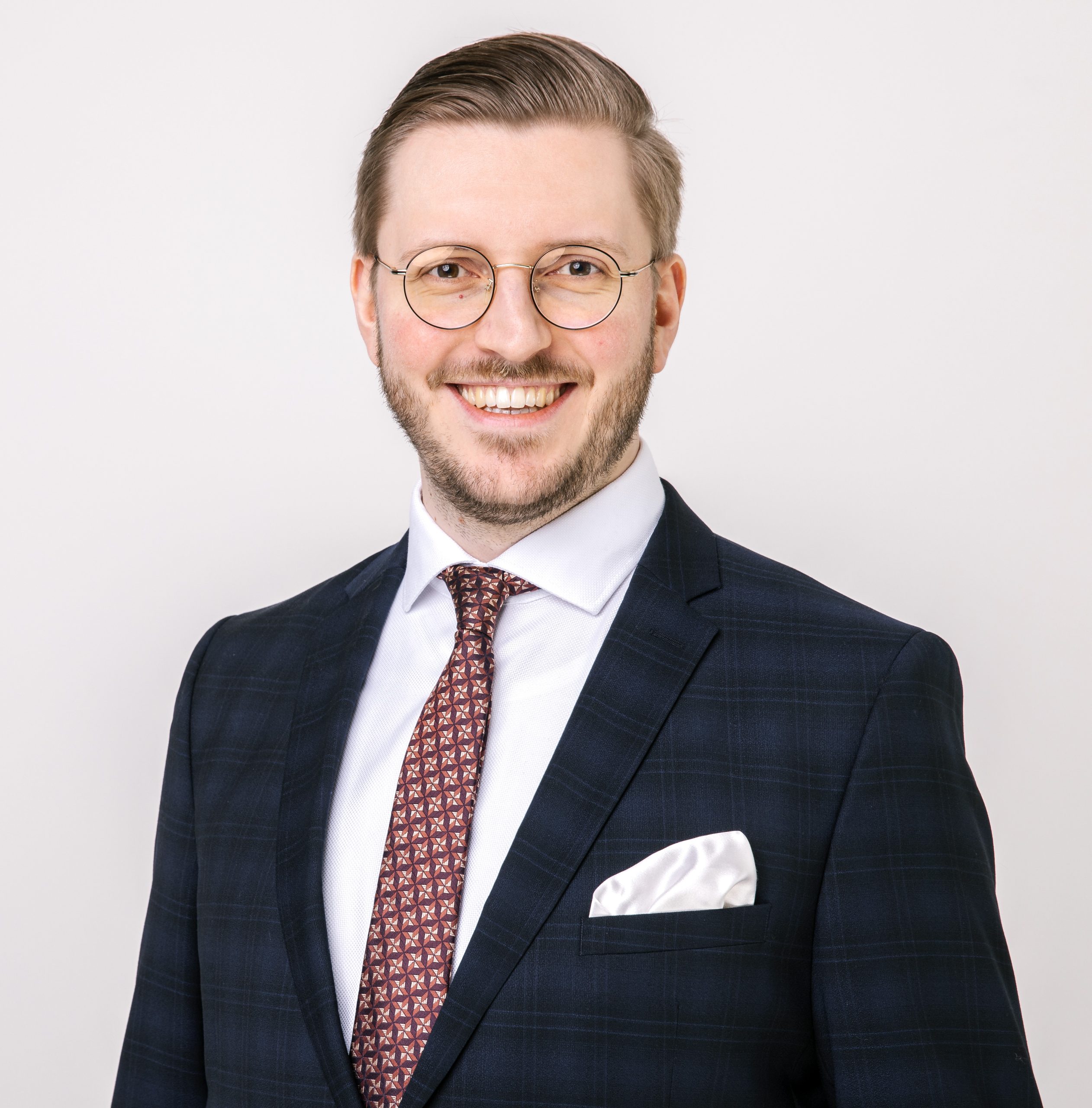
ALEXANDER SCHERER
Das könnte Sie auch interessieren:
So nutzen unsere Kunden Detact!