AI based process control
The intelligent injection mold: A vision becomes tangible
Die Allit Technologie GmbH aus dem rheinland-pfälzischen Bad Kreuznach entwickelt seit über 40 Jahren Werkzeug- und Automatisierungslösungen. In enger Zusammenarbeit mit seinen Kunden realisiert das Unternehmen sowohl einfache als auch komplex verkettete Anlagen, auf denen die verschiedensten Spritzteile und Baugruppen hergestellt werden.
Standard war gestern
Die Allit Technologie entwickelt derzeit ein neuartiges Spritzgussassistenzsystem. Dieses setzt auf die vollautomatische Prozessdatenanalyse mit Künstlicher Intelligenz und kombiniert sie mit einem innovativen, modulartigen Messsystem. Die Anlage bietet Spritzgießern die Gelegenheit, die KI vollumfänglich in ihrer Fertigung mit sehr geringem Aufwand zu implementieren und zu nutzen. Denn: Durch die Kombination mit einem KI-Komplettpaket aus Software und Hardware sowie der Messeinheit können Spritzgießer frühzeitig Prozesstrends erkennen, Ausschuss weitgehend vermeiden und Kosten reduzieren. Aber nicht nur das! Angesichts des vorherrschenden Fachkräftemangels bietet ihnen das System einen weiteren unschätzbaren Vorteil: Das bisher flüchtige Know-how und die Erfahrung der Mitarbeiter wird in einem übergeordneten IT-System gespeichert, das hoch komplexe Prozesse zuverlässig überblickt und Handlungsempfehlungen unterbreitet.
Das Besondere an der neuen Idee ist die hohe Kosteneffizienz: Denn die Messmaschine fungiert als modulare Anlage, die an den verschiedenen Spritzgussanlagen in der Fertigung flexibel wiederverwendet werden kann. Sobald das KI-System mit Hilfe der Messeinrichtung den Fertigungsprozess verstanden und abgebildet hat, kann das KI-System mit dem gespeicherten Prozessmodell arbeiten und ohne die Messmaschine zutreffende Prozessprognosen berechnen. Dieses Einlernen erfolgt zu großen Teilen vollautomatisch und bindet deshalb keine wertvollen Ressourcen.
In den ersten Pilotreihen, die derzeit bei der Allit AG Kunststofftechnik in Bad Kreuznach durchgeführt werden, produziert die Pilotanlage Filtergehäuse und liefert bereits jetzt vielversprechende Ergebnisse.
Fakten statt Bauchgefühl
Im traditionellen Spritzguss benötigen die Maschinenbediener sehr viel Erfahrung und Fingerspitzengefühl, denn sie müssen den laufenden Prozess permanent beobachten und oftmals auch spontan nachsteuern oder kritische Variablen je nach Bedarf anpassen. Denn: Während der Spritzgussfertigung wirken unzählige Faktoren auf den Prozess ein und selbst nach dem Verlassen der Anlage verändern die Bauteile noch ihre Eigenschaften. Erst nach 24 Stunden steht das endgültige Ergebnis fest.
Mit dieser Situation wollte sich die Allit Technologie GmbH, bei der Konzeption ihrer neuen Anlage nicht abfinden. Als Werkzeugbauer kennt das Unternehmen die Herausforderungen seiner Kunden sehr genau und hatte daher auch eine klare Vision: Die neue Anlage sollte die endgültigen Maße und Dimensionen des Werkstückes bereits kurz nach dem Entformen vorhersagen und den gesamten Fertigungsprozess so steuern, dass das Endergebnis den Erwartungen zu 100 Prozent entspricht. Spritzgießer würden so unangenehme Überraschungen vermeiden und vor allem Zeit bzw. Geld sparen.
Angetrieben von dieser Idee entwickelte das Allit-Team zunächst ein modernes 4-Kavitätenwerkzeug mit umfangreicher Sensorik. Die Sensoren liefern dabei wertvolle Daten über den Fertigungsprozess und den Zustand des Werkzeuges. Sensoren und Messsysteme allein gibt es viele, sie sind sozusagen Standard. Aber um heute einen wirklichen Wettbewerbsvorteil zu bieten, müssen sich die Spritzgussanlagen von diesem Standard abheben – beispielsweise durch Künstliche Intelligenz! Daher entwickelte Allit gemeinsam mit den KI-Spezialisten der Symate GmbH eine Lösung, die den klassischen Spritzguss mit Künstlicher Intelligenz verbindet.
Die Pilotanlage geht in die Testphase
Seit einigen Wochen steht die fertige Pilotanlage nun in der Produktionshalle von Allit und alle blicken mit Stolz auf die neuartige Anlage: Rein äußerlich ist sie von einer klassischen Anlage kaum zu unterscheiden, aber schon auf den zweiten Blick fällt die spezielle Messmaschine ins Auge, die direkt vom Entnahmehandling versorgt wird. Und auch die umfangreiche Sensorik zeigt, dass deutlich mehr in der Anlage steckt. Hinzu kommt das alles entscheidende, aber zunächst unsichtbare KI-System ‚Detact‘ von Symate, das die Anlage erst zu dem macht, was sie heute ist: Ein intelligentes Spritzgusssystem, das weit mehr kann, als herkömmliche Anlagen!
Eine neuartige Pilotanlage mit Messmaschine und KI
Mit der Pilotanlage führt Allit zurzeit verschiedene Testreihen durch. Die Kunststoffteile werden gefertigt, im noch heißen Zustand entnommen und automatisch in die modulare Messmaschine gelegt. Diese bildet eine wichtige Grundlage für die KI-gestützte Qualitätssicherung, denn in der Messmaschine werden entscheidende Daten in Form einer 100-Prozent-Stichprobe via Kamera, Laser und Waage gewonnen. Insgesamt erfasst die Messmaschine mehr als 20 Kriterien, die Detact dann vollautomatisch ausliest, analysiert und auswertet. Zusätzlich erfasst Detact noch eine Vielzahl von Maschinen- und Prozessdaten, die über diverse Schnittstellen aus dem Fertigungsprozess übertragen werden. Hierzu gehören bspw. die Anbindung des Messsystems über eine Siemens S7-Steuerung, die Datenerfassung aus der Spritzgussmaschine via Euromap 63 und die Kühlwassermessung via CSV-Kommunikation. Hinzu kommt die Innendrucksensorik mit Analog-/ Digitalwandler-Hardware sowie ein Körperschallsensor für das Predictive Maintenance. Darüber hinaus erfasst Detact auch relevante Informationen aus der Peripherie, wie die Luftfeuchtigkeit und die Temperatur in der klimatisierten Halle, um sie in die komplexe mathematische Analyse einzubinden.
Daten für die KI systematisch sammeln
Die Definition der notwendigen Datenverarbeitungspipelines für die Zusammenführung und Analyse der vielfältigen Daten wird über die Benutzeroberfläche in Detact realisiert. Dabei werden die kontinuierlich eintreffenden Daten vollautomatisch nach dem Prinzip der ‚Stream Analytics‘ ausgeführt. So wird die KI Schritt für Schritt ‚geteacht‘, das heißt sie lernt, Informationen auf die richtige Weise zu analysieren und auszuwerten. Damit das Training und die Modellbildung in Echtzeit umgesetzt werden können, wird jeder Datensatz einzeln hinzugefügt. Durch den hohen Automatisierungsgrad dieses Trainings sind die Anwender klar im Vorteil, denn sobald neue Daten zur Verfügung stehen, fließen sie unmittelbar und ganz automatisch in das Modell ein und verbessern dessen Genauigkeit.
Natürlich dauert es eine Weile, bis eine solide Wissensbasis hergestellt ist. Sobald dieser Status nach rund 2 Wochen erreicht ist, wird die KI als permanenter Begleiter in das System integriert. Nun kann sie eigenständig arbeiten und anhand von Echtzeitinformation Handlungsempfehlungen unterbreiten. Die bis dahin aktive Messmaschine wird für das aktuelle Werkstück nicht mehr benötigt und kann daher für neue Aufgaben an anderen Maschinen eingesetzt werden. Ab jetzt übernimmt die KI die Regie.
Da sich die zu analysierenden Datenmengen hierbei sehr schnell im Bereich von Gigabyte bewegen können, laufen die für die Analyse notwendigen Berechnungen auf mehreren Rechenknoten im hoch performanten und sicheren Detact-Cluster, ohne die Systeme der Spritzgussmaschine zu belasten.
KI gegen den Fachkräftemangel
Die Spritzgussexperten von Allit haben die verschiedensten Ideen miteinander verglichen und Vor- bzw. Nachteile abgewogen. Am Ende steht nun eine Pilotanlage, die ihren Kunden einen echten Mehrwert bietet und zukünftigen Herausforderungen der digitalisierten Produktion gerecht werden kann. Das Team von Allit ist stolz auf das Ergebnis und Udo Gaumann , Geschäftsführer der Allit Technologie GmbH, bringt das zum Ausdruck: „Mit unserer neuen Anlage setzen wir ganz klar auf das Zukunftsthema Industrie 4.0. Aber nicht nur das! Wir bieten gleichzeitig eine Lösung für ein ganz alltägliches Problem: Den Fachkräftemangel! Auf den ersten Blick scheint es hier keine direkte Verbindung zu geben, aber wenn man sich mit Künstlicher Intelligenz und modernem Qualitätsmanagement beschäftigt, wird sehr schnell klar, dass diese Themen perfekt zueinander passen. Für uns lag die Lösung daher schnell auf der Hand. Auch aus diesem Grund haben wir uns für die Zusammenarbeit mit Symate entschieden, denn mit dem KI-System Detact realisieren wir eine leistungsfähige Qualitätsprognose auf Basis von Prozessdaten und wir stellen den Werkern wertvolle Fakten zur Verfügung, mit denen sie arbeiten können. Dabei spielt es praktisch kaum eine Rolle, welche Erfahrung der einzelne Mitarbeiter tatsächlich mitbringt oder mit wie viel Feingefühl er den Prozess im jeweiligen Moment steuert. Am Ende zählen nur die Daten! Mit Detact werden alle Informationen zentral gespeichert und sie gehen selbst dann nicht verloren, wenn bspw. ein Mitarbeiter krank ist oder das Unternehmen verlässt oder wenn Informationen bei Schichtwechsel übermittelt werden müssen.“
Fazit
Mit der KI-gestützten Spritzgussanlage hat die Allit Technologie GmbH eine zukunftsfähige Lösung für Spritzgussunternehmen entwickelt. Diese nutzt Prozessdaten, um die Qualität von Spritzgusserzeugnissen vorherzusagen. Hierfür setzt das Unternehmen auf eine selbst entwickelte, modulare Messmaschine, die an verschiedenen Anlagen flexibel eingesetzt werden kann, um die KI jeweils automatisiert einzulernen. Zur Absicherung will Allit die neue Anlage nutzen, um klassische Methoden der Versuchsplanung (DoE) mit den Möglichkeiten der Künstlichen Intelligenz zu vergleichen und Korrelationen zwischen Prozess- und QS-Parametern zu erkennen. Die dabei gewonnenen Erkenntnisse sollen in die Entwicklung zukünftiger Systeme einfließen.
Derzeit laufen noch die Testreihen, aber die Zahlen sind bereits jetzt vielversprechend. Sollten sich die ersten Ergebnisse bestätigen, möchten die Anlagenbauer der Allit Technologie GmbH gemeinsam mit den KI-Spezialisten von Symate einen Schritt weiter gehen und ein fixes System als integriertes Standardprodukt für den Spritzguss – aber auch für viele andere Anwendungen gemeinsam anbieten.
Mit der einzigartigen Kombination aus klassischer Spritzgussanlage, intelligentem Werkzeug, Messmaschine und KI kann die neuartige Lösung wesentliche Teile der menschlichen Kontrolle über Spritzgussprozess ersetzen, ohne dass die Anwender ein spezielles Know-how benötigen. Angesichts des weithin vorherrschenden Fachkräftemangels würde sich dieses Modell sehr leicht auf andere Branchen übertragen lassen, um auch dort wertvolles Wissen zu digitalisieren und zielgerichtet zu nutzen. Hierzu ergänzt Gaumann: „Wir sind überzeugt, dass das innovative Gesamtsystem im Qualitäts- und Fachkräftebereich Einsparungen von 30% und mehr erzielen wird.“
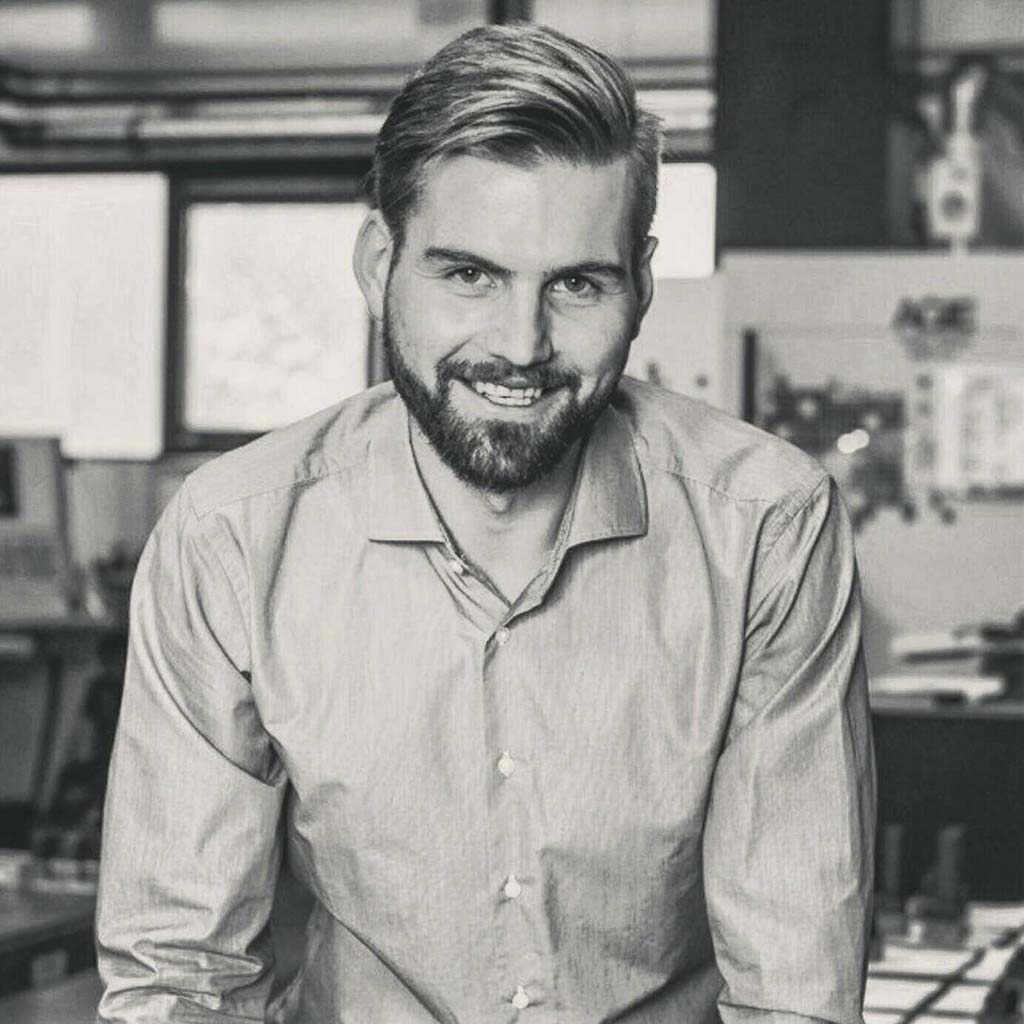
David haferkorn
Das könnte Sie auch interessieren:
So nutzen unsere Kunden Detact!