Detact® erkennt Schwankungen der Blechqualität schon während der Verarbeitung
Entwicklungsprojekt zwischen Thyssenkrupp und der Symate GmbH zeigt die Potenziale und Baustellen von Big Data in der Produktion
Das Thyssenkrupp Stahl-Service-Center (TKSSC) in Radebeul: Auf 16.000 m² Fläche werden hier jährlich rund 140.000 Tonnen Flachstahl verarbeitet. Blechcoils werden in Platinen geschnitten und anschließend an Kunden ausgeliefert. Die technologischen Herausforderungen bestehen darin, trotz schwankender Materialeigenschaften, wie der Sprödigkeit, und komplexer Umformprozesse, eine konstante und hohe Blechqualität zu gewährleisten. Darüber hinaus gilt es, neuen Ansprüchen im Kundenservice gerecht zu werden, wie Deny Winkler, Betriebsleiter TKSSC Radebeul, betont: „Die Anforderungen an die Dokumentation steigen – sowohl an uns als auch an unsere Kunden. Daher möchten wir unseren Kunden noch mehr Informationen über das gelieferte Material bereitstellen.“ Um den Prozess der Blechkonfektionierung transparenter zu machen und weiter zu optimieren, wurden in Kooperation mit den Technologiedaten-Spezialisten der Dresdner Symate GmbH die Möglichkeiten einer automatisierten Datenintegration erprobt. Ziel war es, auf diese Weise die permanent und in großen Mengen anfallenden Daten aus der Produktion nutzbar zu machen, denn sie sind der Rohstoff des Technologiewissens.
Das Team von Symate entwickelt die Software Detact® eine IoT-Plattform für die automatisierte Digitalisierung, Strukturierung und Visualisierung von Technologiedaten und verfügt über ein breites Know-how bei der Direktanbindung von Datenquellen, beispielsweise von Prozessparametern aus Maschinensteuerungen, Messgeräten oder Software-Schnittstellen. Symate ging im Folgenden der spannenden Frage nach, inwiefern sich Aussagen über die Blecheigenschaften schon aus den Parametern einer Blechschneideanlage ableiten lassen. Die Blechqualität als das Ergebnis von Gieß- und Walzprozessen beeinflusst sowohl den Schneidprozess im TKSSC als auch den Umformprozess, der im Anschluss bei den Kunden stattfindet. Indem die Materialeigenschaften schon während des Schneidens erkannt werden, kann der Kunde vorab über diese informiert werden und seine Umformprozesse entsprechend anpassen. So können Fehler vorausschauend vermieden und das Material effizienter genutzt werden Qualitätsmanagement in Echtzeit.
Bei der technischen Umsetzung galt es zunächst alle relevanten Daten in Detact® zu integrieren und deren Analysefähigkeit herzustellen. Dabei handelte es sich einerseits um ERP-Daten für die Beschreibung und Zuordnung der einzelnen Blechcoils, andererseits um Daten aus den SPS-Protokollen der Schneideanlage prozessrelevante Größen wie etwa Schnittmomente oder Servoantrieb. Dazu kamen Feedbackdaten von Kunden aus der Qualitätskontrolle über Typen, Anzahl und Zuordnung von Materialfehlern. Für die Gesamtparameterbetrachtung wurden die Daten anschließend mittels Detact® in Struktur gebracht und mit Kontextinformationen angereichert. Am Beispiel der Anlagenparameter bedeutet dies, dass die Endlossignale der Steuerung auf den laufenden Meter und damit auf das jeweilige Blechcoil bzw. Einzelprodukt zugeschnitten werden mussten, um Bewertungskriterien über die Länge des Blechbandes ermitteln und zuordnen zu können. Die Visualisierung in der Detact®-Benutzeroberfläche ermöglichte im Ergebnis eine Navigation durch die Analyseergebnisse sowie deren statistische Auswertung mittels Mustererkennung oder Festlegung von Grenzwerten. Auf diese Weise ließen sich etwa die walzbedingten Schwankungen der Blechgüte am Bandanfang und -ende erkennen.
Neben den Potenzialen führte das Entwicklungsprojekt aber auch die derzeitigen Baustellen der Digitalisierung vor Augen. So bewertet Deny Winkler vom TKSSC die Kooperation zwar insgesamt als produktiv, „denn die Schwankungen konnten mithilfe der Daten sichtbar gemacht werden, z.B. dass es bei Laufmeter 50 Auffälligkeiten gibt“, schränkt jedoch gleichzeitig ein: „Im Moment gibt es noch viele technische Schwierigkeiten, die den Einsatz der Software in der Praxis verhindern. Durch ein hohes Grundrauschen in den Anlagen und zu wenige Messpunkte sind die Messungen zu ungenau für eine gezielte Datenanalyse. Schon ein durch die Halle fahrender Kran verfälscht die Messdaten erheblich.“ So sei die Datenintegration zukünftig weiterhin attraktiv auch weil genauere Informationen über die Materialbeschaffenheit laut Winkler die Zahl von Reklamationen deutlich reduzieren könnten doch zuvor gelte es, weitere Entwicklungsarbeit und Modernisierungsausgaben, etwa in neue Maschinen und Messtechnik, zu leisten.
Martin Juhrisch, Geschäftsführer der Symate GmbH, zieht ein positives Fazit: „Es war für uns als junges Unternehmen eine weitere lehrreiche Aufgabe, die technische Machbarkeit des Technologiedatenmanagements mit Detact® auch für die anspruchsvolle Anwendung in der Stahlverarbeitung zu erproben, insbesondere mit so einem etablierten Partner wie Thyssenkrupp. Wir konnten dabei neue Wertschöpfungsmöglichkeiten durch Effizienzsteigerungen und ein vernetztes Qualitätsmanagement aufzeigen. Bei der Datenanbindung sind wir natürlich auch immer abhängig von der Verwertbarkeit und Verfügbarkeit der Messdaten.“ Mit anderen Worten: Technologiedatenmanagement braucht eine solide Datengrundlage. Big-Data-Anwendungen können in der Produktion ihre vollen Potenziale erst dann entfalten, wenn Software-Algorithmen und Maschinen-Hardware noch weiter zusammenwachsen. Das Entwicklungsprojekt zwischen dem TKSSC und Symate war dabei ein erster Schritt hin zur Harmonisierung dieser beiden Welten, die nicht länger getrennt betrachtet werden dürfen.
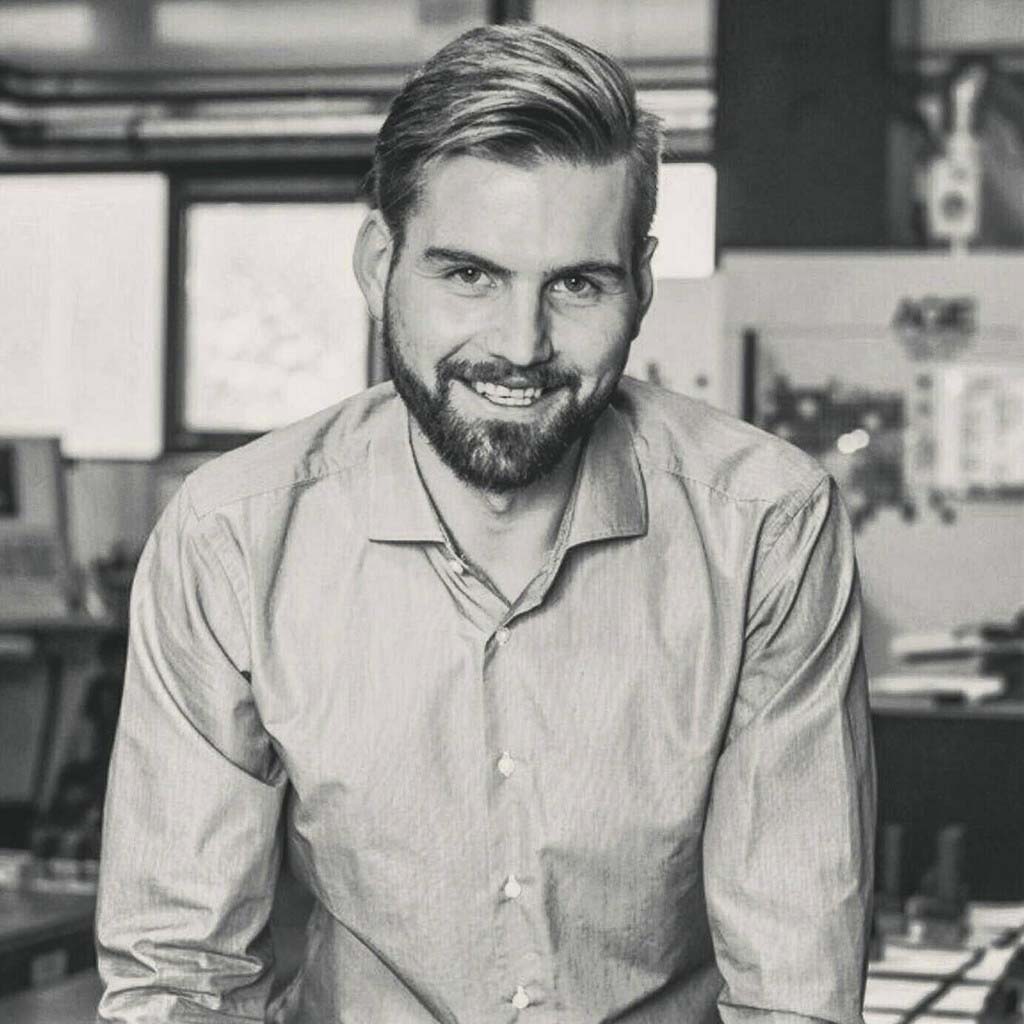
David haferkorn
Das könnte Sie auch interessieren:
So nutzen unsere Kunden Detact!