Data-based optimisation of process and quality
The technology of modern vehicles is increasingly complex and the demands on individual assemblies are continuously rising. Functions that were considered ‘upscale features’ just a few years ago have become ‘standard’ or self-evident at best in the age of digitalisation. But also in terms of quality, the standards are being tightened more and more in a global industry, because the competition has increased significantly. Against this backdrop, German automotive suppliers in particular are challenged to continue to develop innovatively, as they must maintain and further consolidate their market position. They are able to convince above all through high quality and the intelligent networking of sensors or actuators, because this creates new functional scenarios with which the vehicle manufacturers specifically differentiate themselves from one another.
This also applies to Brose, the world’s fourth-largest family-owned automotive supplier. Here, around 25,000 employees develop and manufacture mechatronic systems for vehicle doors and seats as well as electric motors, electronics and much more. Brose components and systems are developed and manufactured at 65 locations in 24 countries and used by around 80 automotive brands worldwide. This is one base of Brose’s strong market position, which the company maintains on a daily basis – f.ex. by a through a clear focus on innovative products of particularly high precision and quality, but also through very lean and economical processes. That is why Brose is constantly investing in new production technologies.
AI for injection moulding
In order to take a significant step forward and continue to secure its technological leadership, Brose has now decided to digitalise parts of its production and reduce possible deviations in the so-called high precision components to a minimum with the help of artificial intelligence (AI): In a current pilot project, the injection moulding of transmission housings for window regulators is being optimised. For this purpose, the company relies on a fully automated production cell with an injection moulding machine from Engel and a CC300 control system. This plant is utilised to around 80 per cent by the gearbox housings alone. In the remaining time, Brose uses the plant to manufacture other products.
In order to make the processes as efficient and transparent as possible, the data provided by means of EM63 and TIG are recorded systematically and around the clock. For this purpose, Brose relies on the Detact AI system as well as on a tactile inline measuring system and – currently still – on extensive measurements accompanying production in quality assurance. With the help of these new technologies, Brose has now developed a particularly sustainable inline quality inspection that gives the injection moulding process significantly more efficiency and transparency…
By the way, you can find a very informative article on this digitalisation project at the Brose plant in Coburg in the trade journal IT & Production (German language).
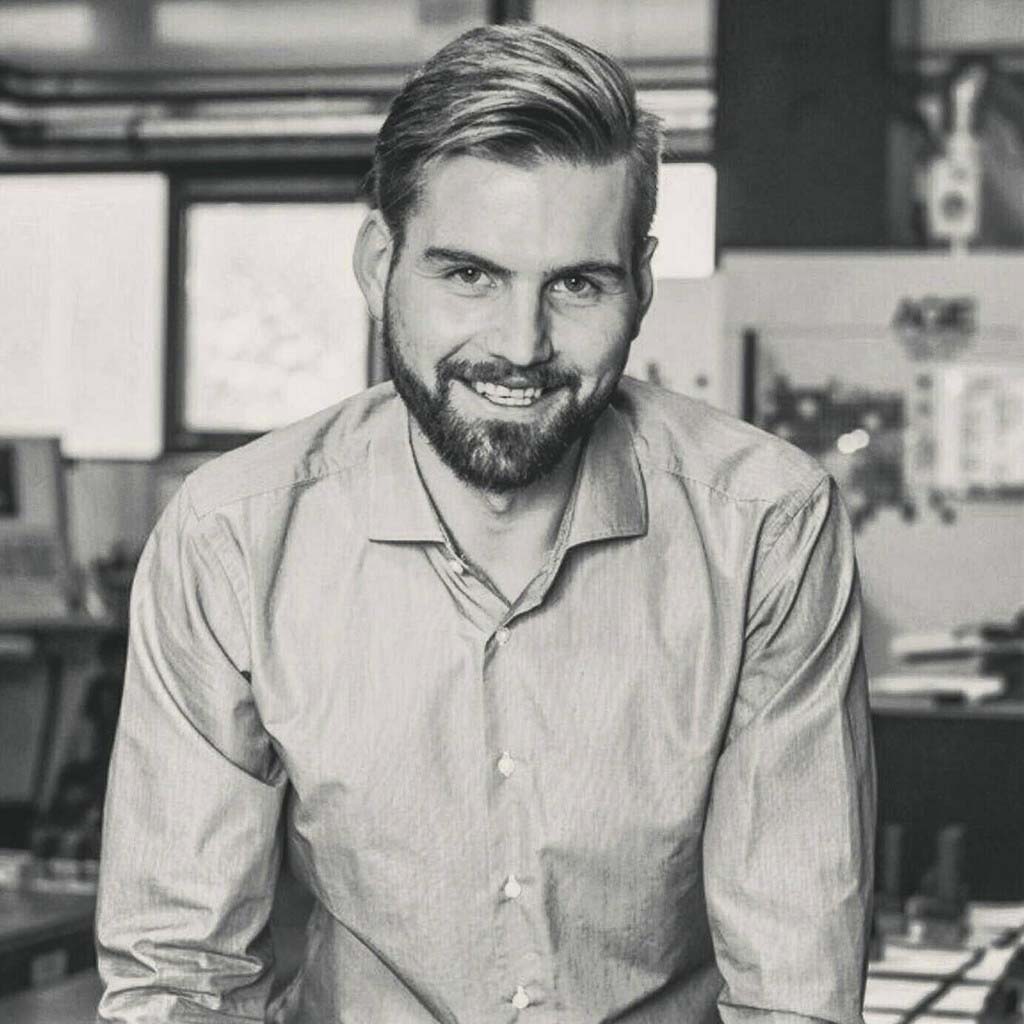
David haferkorn
Das könnte Sie auch interessieren:
So nutzen unsere Kunden Detact!