Hugo Stiehl: Digitaler Zwilling mit KI und Maschinendatenerfassung
Smart Diagnostics – Daten aus der laufenden Produktion systematisch nutzen
Einführung und Zielsetzung der Kooperation zwischen Hugo Stiehl und Symate
Im Werk der Hugo Stiehl GmbH zeigt die Implementierung der IoT-Plattform Detact®, die von der Symate GmbH aus Dresden entwickelt und vermarktet wird, welche Effizienzsteigerungen durch systematisches Technologiedatenmanagement möglich sind. Hugo Stiehl stellt ein großes Spektrum an technischen Kunststoffteilen für die Automobil- und Elektroindustrie bis hin zu kompletten Haushalts- und Gartenartikeln her. Das Ziel der in 2016 gestarteten Zusammenarbeit zwischen Hugo Stiehl und Symate ist es, durch den Einsatz von Detact® Smart Diagnostics die Ausschussquote zu verbessern, allem voran durch den Einsatz automatisierter Analysedienste in Detact im Fall von NIO-Teilen bzw. bei Maschinenstillstand.
Implementierung und Funktionen von Detact
Zuerst mussten die Maschinen lernen, miteinander zu kommunizieren: beispielsweise wurden Daten aus dem Montageprozess über S7-400-Schnittstellen an Detact® Connect angebunden, welche die eingehenden Daten in Echtzeit mit der Cloud synchronisieren. Damit stehen die Anlagenparameter für eine anschließende Analyse und Visualisierung auf der browser-basierten Detact® Benutzeroberfläche zur Verfügung. Besonderer Fokus liegt auf der NIO-Teile-Analyse, um zu untersuchen, welche Gründe es im Einzelfall für hohe Ausschussanteile gibt. Eine Analyse der Ausschussgründe für die Druckprüfung konnte bisher nur mit erhöhtem Aufwand nachvollzogen werden. Hierzu mussten die Rohdaten manuell durchsucht werden. Eine Auswertung der Fehleranteile und Geräte basierende Fehler war kaum bzw. nicht nachvollziehbar darzustellen.
Nutzung von Datenanalyse zur Optimierung von Produktion und Qualität
Natürlich können erfahrene Technologen hier auf ein breites Erfahrungswissen zurückgreifen, doch gerade bei komplexen Prozessen mit einer Vielzahl von Wechselwirkungen ist es notwendig, zusätzlich empirische Daten zu nutzen, um sie umfassender verstehen und beherrschen zu können. Dazu werden sowohl organisatorische Einflussfaktoren, wie Wochentage oder Schichtpläne, als auch Anlagenparameter mit ihren jeweiligen Ist- und Sollwerten kontinuierlich erfasst. Indem sämtliche für die Ausschussquote relevanten Daten miteinander vernetzt und statistisch ausgewertet werden, lassen sich Parameterkombinationen identifizieren, die zuverlässig geringe Ausschussquoten bei konstanter Qualität liefern.
Durch die Einbindung von Qualitätsdaten können wiederum Bauteilschwankungen auf den zugehörigen Ist-Zustand der Maschine zurückverfolgt werden. Die Cloud-Anbindung und automatisierte Datenexploration ermöglichen so ein effektives Lernen im laufenden Prozess bei gleich zeitiger Reduzierung des zeitlichen und personellen Aufwands. Während bisher die Fehlersuche in der Montagelinie und vorgelagerten Spritzguss-Prozessen täglich mehrere Arbeitsstunden von mindestens einem Instandhalter und einem Techniker in Anspruch genommen hat, übernimmt nun Detact einen Großteil der Arbeit. Dabei handelt es sich um speziell auf die jeweilige Prozesskette zugeschnittene Detact Services, welche die Rohdaten so verarbeiten und analysieren, dass der Anwender auf Knopfdruck Unterstützung bei Problemsituationen im Produktionsalltag bekommt.
Aussicht auf zukünftige Entwicklungen und abschließende Betrachtungen
Noch wichtiger ist der Faktor Zeit im Falle eines Maschinenstillstands. Gerade bei großen Produktionsvolumen wie im Hugo Stiehl-Werk Crottendorf zählt jede Minute. Da alle Parameterinformationen, die für die Ursachenforschung im Störfall wichtig sind, per Knopfdruck im System sofort abrufbar sind, sieht Dr. Jens Weller, Geschäftsführer der Symate GmbH, hier große Optimierungspotenziale:
„Wir sind mit Detact® in der Lage, die Stillstandszeit um bis zu 50 % zu reduzieren. Das bedeutet bei einer halben Stunde Zeitersparnis bis zu 500 Teile Mehrausstoß. Darüber hinaus lassen sich durch die Vernetzung und statistische Auswertung der Anlagendaten Parameterwechselwirkungen bei bestimmten Produktionsereignissen wie etwa NIO-Teilen identifizieren. So können Fehlerursachen genauer klassifiziert werden und im Sinne einer vor beugen den Diagnostik kritische Maschinenzustände frühzeitig erkannt und im Idealfall vermieden werden.“
Mit Hilfe von Detact® Smart Diagnostics kann also einerseits das Prozess-Know-how systematisch erweitert werden, auf der anderen Seite erleichtert die Softwareplattform ebenso den Wissenstransfer im Unternehmen. Indem beispielsweise das Know-how erfahrener Mitarbeiter oder eingespielter Schichten auf der Plattform transparent dargestellt und für alle zugänglich gemacht wird, kann auf dies Grundlage eine schnelle und profunde Qualifizierung neuer Mitarbeiter erfolgen.
Der systematische Aufbau von detailliertem Prozess wissen soll dabei jedoch nur ein Entwicklungsschritt sein. Ausblickend auf die weitere Kooperation von Hugo Stiehl und Symate geht der Weg in Richtung Smart Control: aus den mittels Technologiedatenmanagement gewonnenen Erkenntnissen sollen mittelfristig Muster für bestimmte Parameter sowie Parametergruppen abgeleitet werden, um den Anwender noch intensiver zu unterstützten und den Übergang zu autonomeren, selbstregelnden Prozessen zu forcieren.
Fazit und Perspektiven
Michael Neubert, Leiter Prozessentwicklung & Automatisierung Hugo Stiehl GmbH Kunststoffverarbeitung, zeigt sich optimistisch: „Digitalisierungsprojekte in der Produktion sind eine große Herausforderung und Chance zugleich – in der Zusammenarbeit mit der Symate GmbH ist es daher vorteilhaft, dass sowohl das Entwicklerteam als auch die Software Detact® sehr individuell auf die konkreten Anforderungen im Betrieb eingehen können und nicht einfach ein starres, vorgefertigtes Konzept übergestülpt wird. Dadurch entstehen Lösungen, die uns wirklich weiterhelfen.“
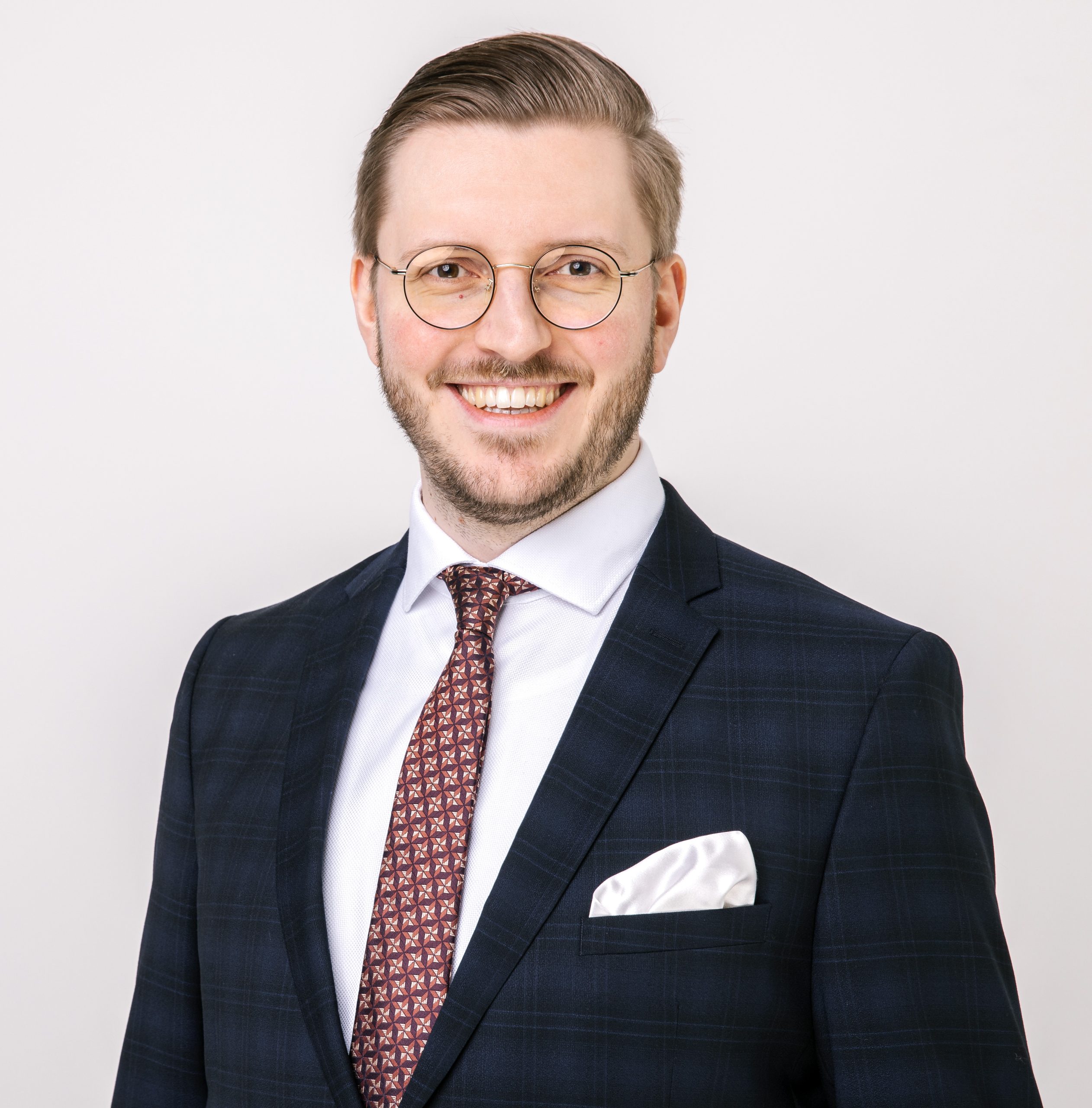
ALEXANDER SCHERER
Das könnte Sie auch interessieren:
So nutzen unsere Kunden Detact!