Künstliche Intelligenz-Software und Big Data: Die treibenden Kräfte hinter Industrie 4.0 bei DLR
Predictive Quality: Hoch effiziente Prozessüberwachung und Qualitätssicherung mit KI von Detact
Predictive Quality: Hoch effiziente Prozessüberwachung und Qualitätssicherung mit KI von Detact
Das Deutsche Zentrum für Luft- und Raumfahrt (DLR) gehört zu den bekanntesten Forschungseinrichtungen Deutschlands. Die Forschung am niedersächsischen DLR-Standort Stade konzentriert sich auf die Herstellung von großskaligen und komplexen Bauteilen in hochproduktiven Faserablageverfahren. Hier wird der Multimaterialleichtbau unter industrienahen Bedingungen erforscht. Mit Hilfe einer sogenannten GroFi®-Anlage zur Herstellung von großflächigen, hochintegralen Bauteilen in automatisierten Fiber-Placement-Verfahren (AFP) werden neue Technologien und Verfahren entwickelt, die eine effiziente Fertigung ermöglichen. Automatisierte Fiber-Placement-Verfahren kommen beispielsweise für den Bug- und Cockpitbereich des Dreamliner 787 von Boeing sowie bei Flügel- und Rumpfstrukturen des Airbus A350 zum Einsatz.
Um anwendungsnahe Lösungen zu entwickeln und die Prozesse beim AFP-Verfahren perfekt überwachen zu können, implementiert das DLR in der GroFi®-Anlage nun die künstliche Intelligenz eines Softsensors. Dieser vergleicht Simulationsprozesse mit den Daten aus der realen Fertigung und prognostiziert die Qualität der fertigen Bauteile. Mit Hilfe dieses neuen Systems wollen die Forscher mögliche Abweichungen auf der Basis von vorhandenen Prozess- und Qualitätsdaten erkennen sowie rechtzeitig vor dem Eintreten von Fehlern zielgerichtet Maßnahmen ergreifen.
Der Softsensor: Künstliche Intelligenz für die vollautomatische Quality-Prediction
Der Softsensor wird derzeit von der Dresdner Symate GmbH auf der Basis der KI-Software Detact entwickelt. Er soll nach den Vorgaben des DLR als ergänzendes Onlineüberwachungs-Tool an der Forschungsanlage eingesetzt werden und die Abhängigkeit von Messgrößen zu einer Zielgröße abbilden. Dies wäre mit rein physikalisch-basierten Sensordaten kaum realisierbar. Stattdessen arbeitet der Softsensor wie eine Simulation und erweitert die aus realen Sensoren stammenden Informationen durch Simulationsdaten.
Nach diesem Prinzip arbeitet auch der KI-basierte Detact-Softsensor von Symate. Er verwendet einen speziellen Auswertealgorithmus, der die erforderlichen Zielgrößen aus den vorhandenen Daten in Echtzeit errechnet. Sobald der Softsensor beim DLR in Stade eingerichtet ist und die Anlage in der Symate-Cloud abgebildet wurde, soll er mit der Simulation interagieren und das Qualitäts- und Toleranzmanagement des DLR in Stade durch seine künstliche Intelligenz auf ein neues Level heben: Die vollautomatische Inline-Quality-Prediction. Auf dieser Basis kann das DLR während der noch laufenden Produktion valide Qualitätsvorhersagen treffen und die Ablegeprozesse in einem vorab definierten Fenster überwachen. Das DLR nennt dies eine ‚in-situ‘-Strukturbewertung. Zudem lernen die Forscher die Grenzen von realistischen Prozessfenstern kennen und können tolerierbare Abweichungen im System hinterlegen.
Um diese in-situ-Strukturbewertung zu ermöglichen, sind kleinere Anpassungen im System des DLR erforderlich. So muss der Detact-Sensor bspw. mit einem optischen Messsystem und den Simulationsdaten aus der DLR-Datenbank verbunden werden. Hieran wird in einem aktuellen Projekt gearbeitet. Ist das geschehen, empfängt der Softsensor alle relevanten Daten, wertet sie live aus und prognostiziert die Qualität der laufenden Produktion kontinuierlich. Zudem vergleicht die KI in Detact alle verfügbaren Informationen aus dem realen Prozess mit den Simulationsdaten. Damit werden Wissenslücken automatisch geschlossen und das System prognostiziert die erforderlichen Parameter für zukünftige Prozesse.
Hierzu erklärt Falk Heinecke, der für den Einsatz des neuen Softsensors verantwortliche Wissenschaftler des DLR: „Unsere Forschungsanlage ist für den Bau großflächiger, hochintegraler Leichtbaustrukturen perfekt geeignet, denn sie vereint die modernsten Technologien zur Herstellung von Leichtbauteilen. Schon seit einigen Jahren verfolgen wir hoch innovative Ansätze für eine optimierte, reproduzierbare, produktive und gleichzeitig kosteneffiziente Fertigung. Dabei können wir sehr gute Erfolge vorweisen. Mit Detact können wir nun einen Schritt weiter gehen und die neue Produktionstechnologie auf dem Weg zu selbstregulierenden Prozessen erweitern. Mit diesem zusätzlichen Baustein schaffen wir eine intelligente Anlagensteuerung nach dem Vorbild der Industrie 4.0, von der Bauteilhersteller, Anlagenlieferanten und Materialhersteller verschiedener Branchen profitieren. In einem ersten Schritt werden wir das neue System für die Herstellung von Flugzeugstrukturen einsetzen. Von dem automatisierten Fiber-Placement-Verfahren versprechen wir uns deutliche Optimierungen bei der Geschwindigkeit und Qualität der Prozesse.“
So funktioniert das AFP-Verfahren
Für das AFP-Verfahren werden sogenannte ‚Tows‘ – spezielle Materialbänder mit wenigen Millimetern Breite – von Robotern Bahn für Bahn ‚nebeneinander‘ und Lage für Lage ‚übereinander‘ gelegt, um die Bauteilgeometrie abzubilden. Die einzelnen Bahnen sind nicht immer gerade, sondern können auch bogenförmig gelegt werden. Sind die Bahnen gelegt, werden sie in einem Autoklav verpresst und ausgehärtet.
Aufgrund der individuellen Geometrie der einzelnen Bauteile entstehen Lücken zwischen den Bändern. Auch Überlappungen, Verdrehungen oder andere Fertigungsabweichungen können gelegentlich auftreten. Derartige Merkmale beeinflussen die Qualität der Bauteile und müssen überwacht werden. Bei einem großen Bauteil wie einem Airbus-Flügel entfallen derzeit allein auf die Inspektion, Reparatur und Nacharbeit dieser Ablegefehler mehr als 30 Prozent der gesamten Fertigungszeit aus. Das ist ein erheblicher Aufwand.
Selbstregulierende Prozesse und intelligente Qualitätsprognose
Um die Standzeiten aufgrund von Reparatur und Nacharbeit zu minimieren, arbeitet das DLR mit einer Inline-Qualitätsüberwachung sowie an Simulationsmethoden, die den Ablegeprozess sehr detailliert abbilden. Das DLR entschied sich, die GroFi®-Anlage um den neuen Detact-Softsensor zu ergänzen, denn dieser verbindet die Simulation mit dem realen Prozess und erkennt mögliche Auswirkungen von Abweichungen im Ablegeprozess. Der Softsensor liest die verschiedensten Datenquellen fertigungsbegleitend aus und verknüpft sie vollautomatisch mit den Simulationsergebnissen aus der sogenannten Effects of Defects-Datenbank (‚EoD-DB‘) des DLR. Die EoD-DB enthält sogenannte Knock-Down Faktoren für die Steifigkeit und Festigkeitseigenschaften des Laminats. Auf dieser Basis können die Forscher entscheiden, ob die im Prozess auftretenden Abweichungen außerhalb der zulässigen Spezifikation bzw. der strukturellen Toleranz liegen oder nicht.
Mit diesen Daten wird die Detact-KI systematisch arbeiten und Schritt für Schritt ein eigenes Modell aufbauen, das sowohl interne als auch externe Einflüsse auf die Bauteilqualität enthält. Ist das geschehen, werden die Fehlerquellen und mögliche Defekte an einem 3D- bzw. CAD-Modell visualisiert.
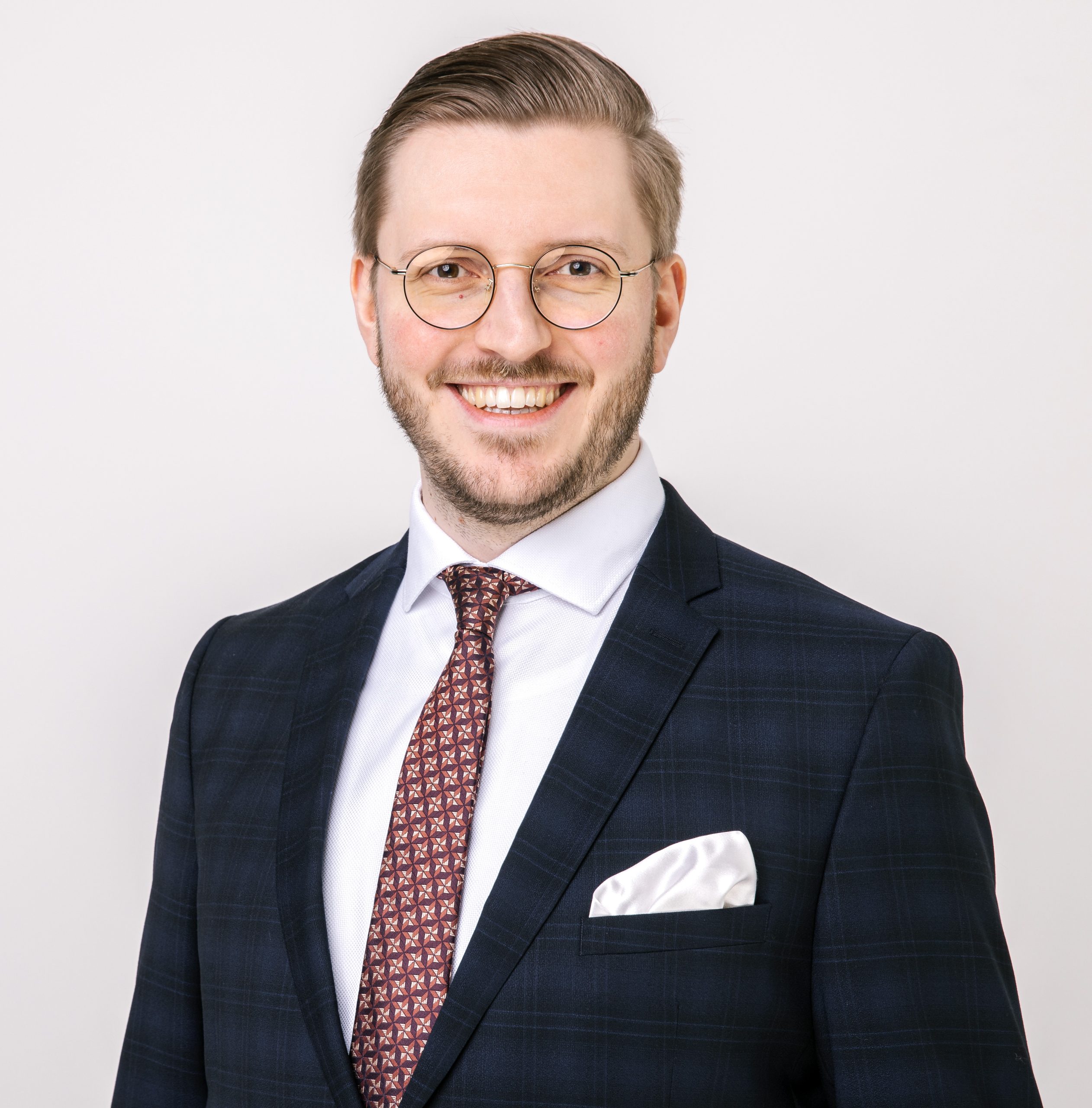
ALEXANDER SCHERER
Das könnte Sie auch interessieren:
So nutzen unsere Kunden Detact!