DGH Group optimiert Produktion mit innovativem Manufacturing Execution System und KI-Anwendungen
Technologiedatenmanagement als Herausforderung und Chance
- Technologischer Fortschritt, ökologisches Bewusstsein, demografische Veränderung – die Digitalisierung technologischer Daten gilt inzwischen als ein wesentlicher Erfolgsfaktor beim Druckgießen
In einer Roadmap wurde das Thema Technologiedatenmanagement (TDM) skizziert und ein Projekt in Zusammenarbeit mit der DGH Group – DGH Heidenau GmbH & Co. KG, Dohna, und der Symate GmbH, Dresden, umgesetzt. Sowohl die anwenderorientierte Softwareentwicklung als auch methodische Änderungen in Prozessen, Systemen, Strukturen, Ressourcen und der Kultur offerieren Transparenz über Produkte und Prozesse in Echtzeit. Dies wurde anhand eines Neuauftrags von Druckgussbauteilen eines Automobilherstellers im Premiumsegment erfolgreich nachgewiesen. Die Ergebnisse zeigen: Das TDM liefert einen erheblichen Beitrag zur Wirtschaftlichkeit und Kundenzufriedenheit. Ein neuer Standard bietet eine Erweiterung des Knowhows und greifbaren Kundenmehrwert.
Smart Die Casting – Wo Tradition und High-Tech verschmelzen
Entlang traditioneller Erfolgsfaktoren von Gießereien ist festzustellen, dass Transparenz zukünftig mehr ist als das Ergebnis eines guten Controllings. Darüber hinaus führen wachsende Kundenansprüche und Produktanforderungen aus der Automobilindustrie zu technologischen Herausforderungen in der Druckgussbranche. Weiterentwicklungen von Werkstoffen, Fertigungsverfahren und Betriebsmitteln sowie ihre vielfältigen Wechselwirkungen sollen im betrieblichen Alltag die Wirtschaftlichkeit und Kundenzufriedenheit erhöhen. Eine Potenzialanalyse führte zu der Frage, inwieweit man mithilfe eines Technologiedatenmanagements das Know-how über den Produktlebenszyklus ausbauen kann. Ausgehend von der Vision, dass in einer Smart Factory smarte Produkte gefertigt und den Kunden auch smarte Services offeriert werden, erstellten die Projektpartner eine Roadmap, in der die wesentlichen Ziel- und Aufgabenstellungen festgelegt sowie Aufwand, Nutzen und Bewertungsgrößen definiert wurden. Basis dabei ist der nachhaltige Umgang mit großen Datenmengen in komplexen Wertschöpfungsketten, idealerweise im System Kunde-DGH-Lieferant und in Echtzeit.
Anforderungen, Ausgangssituation und Ziele des Projekts
Im Vorfeld des Projekts wurden Anforderungen definiert, um Prozesse nachhaltig zu gestalten:
- Lückenlose Bauteilverfolgbarkeit in Bezug auf Fertigungsparameter und Qualitätskennwerte: bauteilgenaue Verknüpfung von Technologie- und Qualitätsdaten, Steigerung der Fertigungstransparenz
- Abbildung des Auftragsfortschrittes: fertigungsschrittgenaue Abbildung von Kennzahlen
- Analyse von Parameterverläufen gießtechnologischer Einflussgrößen und Mustererkennung: Prozessüberwachung, Erkennen von Ausreißern und Verstehen der Ursache-Wirkungszusammenhänge, Abgabe von Parameterprognosen
- Abbildung technischer Einflussgrößen: Identifizieren von Störursachen, Minimieren von Inbetriebnahmezeiten, Zykluszeiten sowie Ausschussfehlern
- Analyse komplexer Parameterzusammenhänge und Wechselwirkungen: Identifizieren der Einflüsse von Umgebungs- und Fertigungsparametern entlang der gesamten Fertigungskette
- Integration von Energie- und Betriebsstoffdaten: Analyse von Einsparpotenzialen
Vor Projektbeginn wurden in der DGH Group bereits große Mengen an Daten archiviert. Diese lagen teilweise im Rohformat vor, isoliert in verschiedenen Datenquellen. Die Nutzung von aggregierten Daten für die aufgeführten Recherche- und Analyseaufgaben waren vor diesem Hintergrund sehr zeitaufwendig, örtlich beschränkt und teilweise nicht möglich. Im Jahr 2015 entschloss sich die DGH daher, diese Herausforderungen anzunehmen und mit dem System Detact der Symate GmbH ein webbasiertes TDM-System einzuführen.
Projektablauf und Herausforderungen
Die Einführung des TDM-Systems erfolgte in den vier Schritten Konzeption, Datenanbindung, Datenverarbeitung sowie Analyse & Steuerung. Um schnell nachvollziehbare Ergebnisse zu erzielen, wurde der Umfang der vier Schritte grundsätzlich klein gehalten, das System jedoch durch einen mehrfachen Durchlauf der Phasen (Iteration) schrittweise ausgebaut. Dabei dauerte eine Iteration im Projektverlauf jeweils zwischen zwei und vier Monaten.
Konzeption
Um das Ziel einer lückenlosen Bauteilverfolgbarkeit mit der eindeutigen Nachvollziehbarkeit von Bauteil-ID, Technologiedaten und Bewertung der Qualitätsgüte zu erreichen, erfolgte zu Beginn eine Analyse des DGH-Druckgießprozesses. Hierfür wurde der Fertigungsprozess zunächst als Prozessmodell visualisiert. In der ersten Iteration erfolgte eine Begrenzung auf die Druckgießzelle, in späteren Durchläufen wurde das Modell schrittweise in der „Breite“ ausgebaut. So wurden bis heute die Fertigungsschritte entsprechend Bild 3 implementiert. Darauf aufbauend wurden jeweils Anforderungen und Ziele für die anstehende Iteration definiert.
Anbindung Datenquellen
Die zweite Phase umfasst die Anbindung aller für den Iterationsschritt relevanten Datenquellen. Hierfür wurden bestehende Schnittstellen verwendet (primär der zyklische Dateiexport durch die Anlagen selbst). Für jede Datenquelle wurden in der Software sogenannte Detact-Treiber konfiguriert. Diese von der Symate GmbH entwickelten Softwarebausteine kommunizieren mit den Datenquellen und verarbeiten die dort abgerufenen Informationen.So können Daten unterschiedlichster Struktur verarbeitet werden. Auf diese Weise gelangen die laufend anfallenden Prozessdaten automatisiert ins System, werden auf dem Weg interpretiert und so analysefähig gemacht. In weiteren Projektdurchläufen erfolgte der schrittweise Ausbau des DGH-internen IT-Netzwerks. Sofern es erforderlich schien, wurde zusätzlich robuste Erfassungstechnik (Kameratechnik, Messeinrichtungen) nachgerüstet und wiederum entsprechende Detact-Treiber konfiguriert.
Datenverarbeitung
Um eine prozessübergreifende, lückenlose Analyse zu ermöglichen, war zunächst der Aufbau eines integrierten Datenbestands zwingend notwendig. Hierbei galt es, nicht nur einmalig eine bestimmte Datenmenge zusammenzuführen, sondern eine dauerhafte Lösung aufzubauen, mit der die gesammelten Daten automatisiert synchronisiert werden können. Dies erfolgte auf Basis der Detact IoT-Architektur (Internet of Things). Als besondere Herausforderung ergab sich die an einer Fertigungslinie nicht verfügbare Bauteil-ID (zeitbezogene Erfassung). Dadurch mussten die Daten zeitbezogen zusammengeführt werden, was sich durch unterschiedliche Abtastraten und mitunter stetig abweichende Uhrzeiten der Datenquellen (Druckgießmaschine, Peripherie, Prüfsysteme) als schwierig erwies. Diese Herausforderung konnte durch den kombinierten Einsatz intelligenter mathematischer Verfahren, u. a. zur Erkennung zeitlicher Muster in den Daten, gelöst werden.
Im Ergebnis werden nun im laufenden Produktionsbetrieb alle relevanten Daten gesammelt und automatisiert zu einem integrierten Datenbestand zusammengeführt. Daten werden dauerhaft dokumentiert und stehen sowohl für unmittelbare (Echtzeit-)Analysen als auch für die Recherche und den Vergleich mit zurückliegenden Fertigungsinformationen zur Verfügung.
Analyse & Steuerung
Neben der IoT-Architektur stellt Detact auch umfangreiche Analysefunktionen bereit. Für die Anwendung bei DGH sollten mathematische Funktionen jedoch gekapselt werden, um ingenieurgerechte Recherche- und Visualisierungsoberflächen bereitzustellen. Hierfür wurde Detact im Rahmen der vierten Projektphase jeweils mit Hilfe der im System integrierten Customizingsprache schrittweise erweitert. Auf diese Weise entstanden für die Nutzergruppen Logistik, Instandhaltung, Produktion sowie Technologie individuelle Funktionen mit einem unterschiedlichen Detaillierungsgrad.
Ergebnisse und Nutzen
Im Rahmen des Projektes wurden mit dem System Detact Technologiedaten gesammelt, verarbeitet und analysiert. Mit seiner Unterstützung konnte eine Steigerung der Gesamtanlageneffektivität von >10 % aufgezeigt werden. Dabei wurden die bestimmenden Faktoren Verfügbarkeit, Leistung und Qualität gezielt optimiert. Der Steigerung des Verfügbarkeitsfaktors wurde eine lückenlose Historie von Maschinenereignissen (Warnungen, Störungen) zugrunde gelegt. Ungeplante Stillstände werden klassifiziert sowie bis auf die kleinste Maschineneinheit nachvollzogen. Zusätzlich wird das Nutzerverhalten des Anlagenbedieners hinsichtlich Warnungen und Störungen betrachtet, abzuleitende Maßnahmen werden standardisiert und fließen gezielt in das Total Productive Maintenance (TPM)-Konzept des Unternehmens ein. Darüber hinaus werden auch Kurzstillstände infolge von technischen Störungen ausgewertet, um deren Einfluss auf den Leistungsfaktor der Maschine zu minimieren. Die echtzeitgenaue Darstellung von Taktzeiten aus dem Fertigungsprozess, entsprechenden Prüfzyklen sowie vielfältigen Technologiedaten eröffnen die Möglichkeit, bei Problemen kurzfristig zu reagieren. Die Verknüpfung von Betriebsmittel- und Qualitätsdaten mit einer eindeutigen Bauteil-ID und ihrer echtzeitgenauen Visualisierung entlang der gesamten Fertigungskette erlaubt sowohl eine detailgetreue als auch eine zügige FehlerUrsachen-Analyse als Basis der Qualitätssteigerung. Mit der Unterstützung von Detact sowie anwenderspezifischen Analysefunktionen (Nutzergruppen) konnte der Personalaufwand sowie die Fehlerhäufigkeit durch manuelle Verarbeitung und Auswertung qualitätsrelevanter Daten deutlich reduziert werden. Diese werden bauteilgenau aufbereitet und können projektbegleitend in Form einer Bauteilhistorie und eines Bauteilbriefes ad hoc abgerufen werden. Mit der Visualisierung der Bauteilhistorie können Durchlaufzeiten detailliert visualisiert werden. Der Vergleich von fertigungsschrittgenauen, realen Produktions- und Prüfzeiten mit den Vorgaben unterstützt die effizientere Gestaltung von Fertigungsabläufen. Weiterhin bietet das Tool mit seinen spezifischen Analysen bereits vor dem Produktionsstart, in der Produkt- und Prozessentwicklung sowie in den Bemusterungsphasen der Bauteilanläufe Unterstützung. Hierbei wird der Einfluss von einem oder mehreren Maschinenereignissen und Technologieparametern sowie deren Zusammenspiel auf das Qualitätsergebnis dargestellt. Analysen über längere Zeiträume können auch Rückschlüsse zu saisonalen Einflüssen auf den Gießprozess geben. Komplexe technologische Ursache-Wirkungszusammenhänge werden so transparent dargestellt und der daraus generierte Know-how-Zuwachs als „Lessons Learned“ (Gewonnene Erkenntnisse) für nachfolgende Produkte und Risikoanalysen genutzt. Das Aufzeigen von Energie- und Betriebsstoffeinsparungen ist ebenfalls durch die Digitalisierung der dafür relevanten Daten in der Gießzelle transparent gestaltet worden. Hier können deutliche Kosteneinsparpotenziale aufgezeigt werden. Durch die erzielte Transparenz sowie die Verknüpfung relevanter Parameter und die Auswertung auch größerer Datenmengen ist es gelungen, ganzeinheitlich Optimierungspotenziale für die Gesamtanlageneffektivität sowie für Energie- und Betriebsstoffverbräuche auf zu zeigen und damit einen positiven Effekt für die Wirtschaftlichkeit sowie die Umwelt und den Energieverbrauch zu erzielen.
Zusammenfassung und Ausblick
Im Rahmen des Pilotprojekts wurden die ersten Schritte zu einem erfolgreichen Technologiedatenmanagement aufgezeigt, welches insbesondere in Bezug auf Produktinformationen einen erheblichen Kundenmehrwert liefert. Datentransparenz und der gezielte Einsatz von TDM führen zu vielfältigem Nutzen. Der neue Ansatz führt bereits in Entwicklungs- und Planungsprozessen sowie in Produktionsabläufen zu größerer Effizienz. Technische, organisatorische und auch kulturelle Herausforderungen lösten eine abwechslungsreiche Berg- und Talfahrt aus. Rückblickend ist festzustellen, dass mit dem Technologiedatenmanagement eine wachsende Unternehmenskompetenz, eine „Lernende Organisation”, einhergehen muss. Weitere Schwerpunkte werden ausgebaut, beispielsweise auf dem Feld der robusten Informationstechnik und Automatisierung. Außerdem gilt es, die Wertschöpfung in ihrer Tiefe weiter in das System einzubinden sowie mobile „Reports“ zu gestalten. Auf dem Weg zur Smart Factory offeriert die DGH Group einen TDMStandard – die Voraussetzung für die Weiterentwicklung zum intelligenten Gesamtsystem.
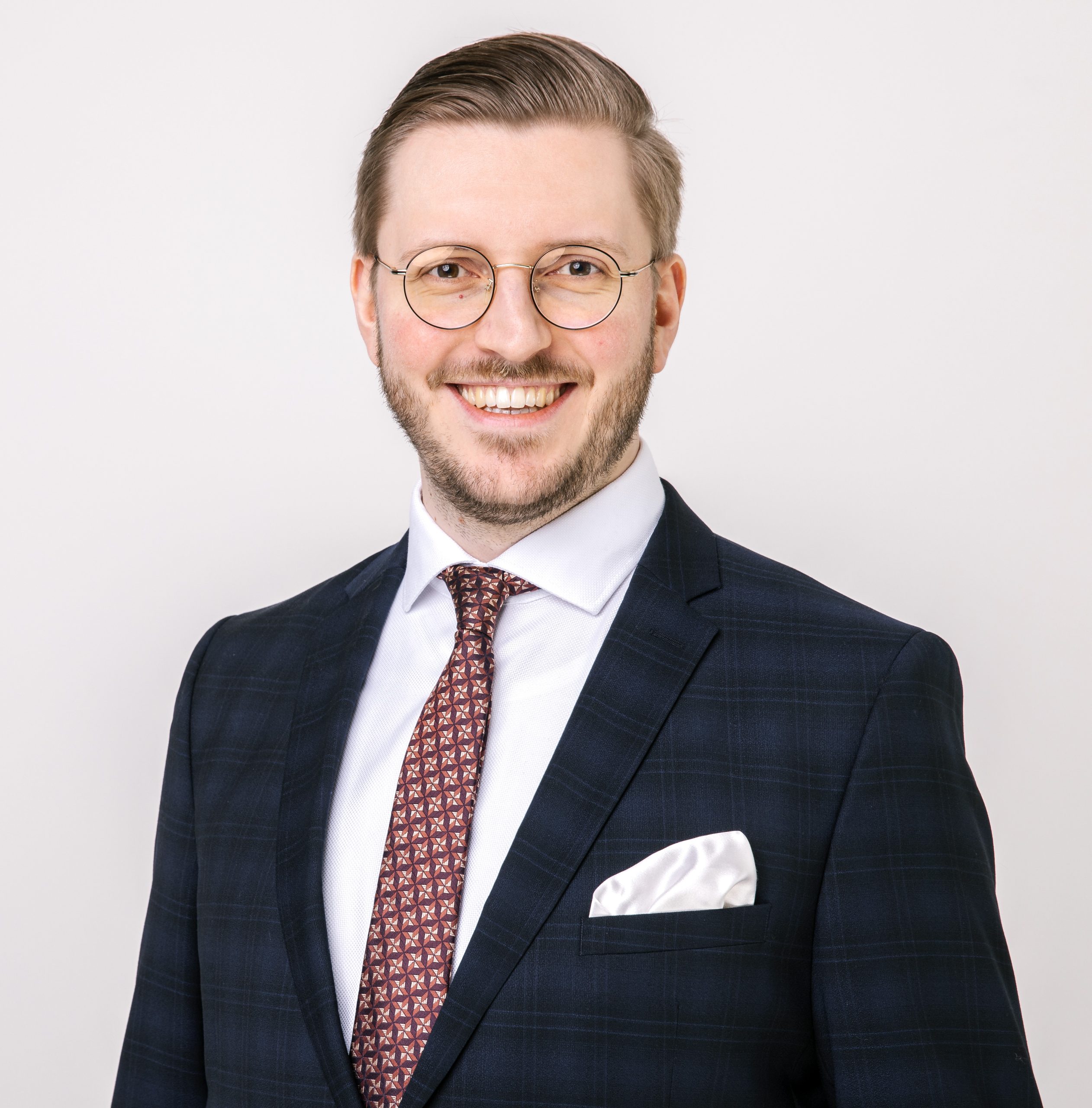
ALEXANDER SCHERER
Das könnte Sie auch interessieren:
So nutzen unsere Kunden Detact!