KI-Integration in der Brose-Produktion: Erweiterte BDE- und MES-Funktionen
Datenbasierte Optimierung von Prozess und Qualität
Die Technik unserer modernen Fahrzeuge wird immer komplexer und die Anforderungen an einzelne Baugruppen steigen kontinuierlich. Was noch vor wenigen Jahren als ‚gehobene Ausstattung‘ galt, ist im Zeitalter der Digitalisierung allenfalls ‚Standard‘ oder selbstverständlich geworden. Aber auch in Sachen Qualität werden die Maßstäbe im globalen Technologiewettbewerb immer weiter angezogen, denn die Konkurrenz hat deutlich zugenommen. Vor diesem Hintergrund sind vor allem die deutschen Automobilzulieferer herausgefordert, sich innovativ weiter zu entwickeln, denn sie müssen ihre Marktposition behaupten und weiter festigen. Dabei können sie vor allem durch hohe Qualität und die intelligente Vernetzung von Sensoren bzw. Aktuatoren überzeugen, denn so entstehen neue Funktionsszenarien, mit denen sich die Fahrzeughersteller gezielt voneinander abheben.
Das gilt auch für Brose, den weltweit viertgrößten Automobilzulieferer in Familienbesitz. Hier entwickeln und fertigen rund 25.000 Mitarbeiter mechatronische Systeme für Fahrzeugtüren und -sitze sowie Elektromotoren, Elektronik und vieles mehr. Die Komponenten und Systeme von Brose werden an 65 Standorten in 24 Ländern entwickelt und hergestellt sowie von rund 80 Automobilmarken weltweit eingesetzt. Damit hat Brose eine sehr starke Marktposition, die das Unternehmen tagtäglich neu behauptet – bspw. durch einen klaren Fokus auf innovative Produkte von besonders hoher Präzision und Qualität, aber auch durch sehr schlanke und wirtschaftliche Prozesse. Daher investiert Brose immer wieder in neue Fertigungstechnologien.
KI für den Spritzguss
Um einen signifikanten Schritt voran zu gehen und die Technologieführerschaft weiterhin zu sichern, hat sich Brose nun entschieden, Teile seiner Fertigung zu digitalisieren und mögliche Abweichungen an den sogenannten High Precision Components mit Hilfe von künstlicher Intelligenz (KI) auf ein Minimum zu reduzieren: In einem aktuellen Pilotprojekt wird der Spritzguss von Getriebegehäusen für Fensterheber optimiert. Hierfür setzt das Unternehmen auf eine vollautomatische Fertigungszelle mit einer Spritzgießmaschine der Firma Engel und einer CC300-Steuerung. Diese Anlage wird allein von den Getriebegehäusen zu rund 80 Prozent ausgelastet. In der verbleibenden Zeit nutzt Brose die Anlage, um andere Produkte herzustellen.
Um die Prozesse möglichst effizient und transparent zu gestalten, werden die mittels EM63 und TIG bereitgestellten Daten systematisch und rund um die Uhr erfasst. Hierfür setzt Brose auf das KI-System Detact sowie auf ein taktiles Inline-Messsystem und – zurzeit noch – auf umfangreiche produktionsbegleitende Messungen in der Qualitätssicherung. Mit Hilfe dieser neuen Technologien hat Brose nun eine besonders nachhaltige Inline-Qualitätsprüfung entwickelt, die dem Spritzgießprozess deutlich mehr Effizienz und Transparenz verleiht…
Einen sehr informativen Beitrag zu diesem Digitalisierungsprojekt im Brose-Werk Coburg finden Sie übrigens in der Fachzeitschrift IT & Production.
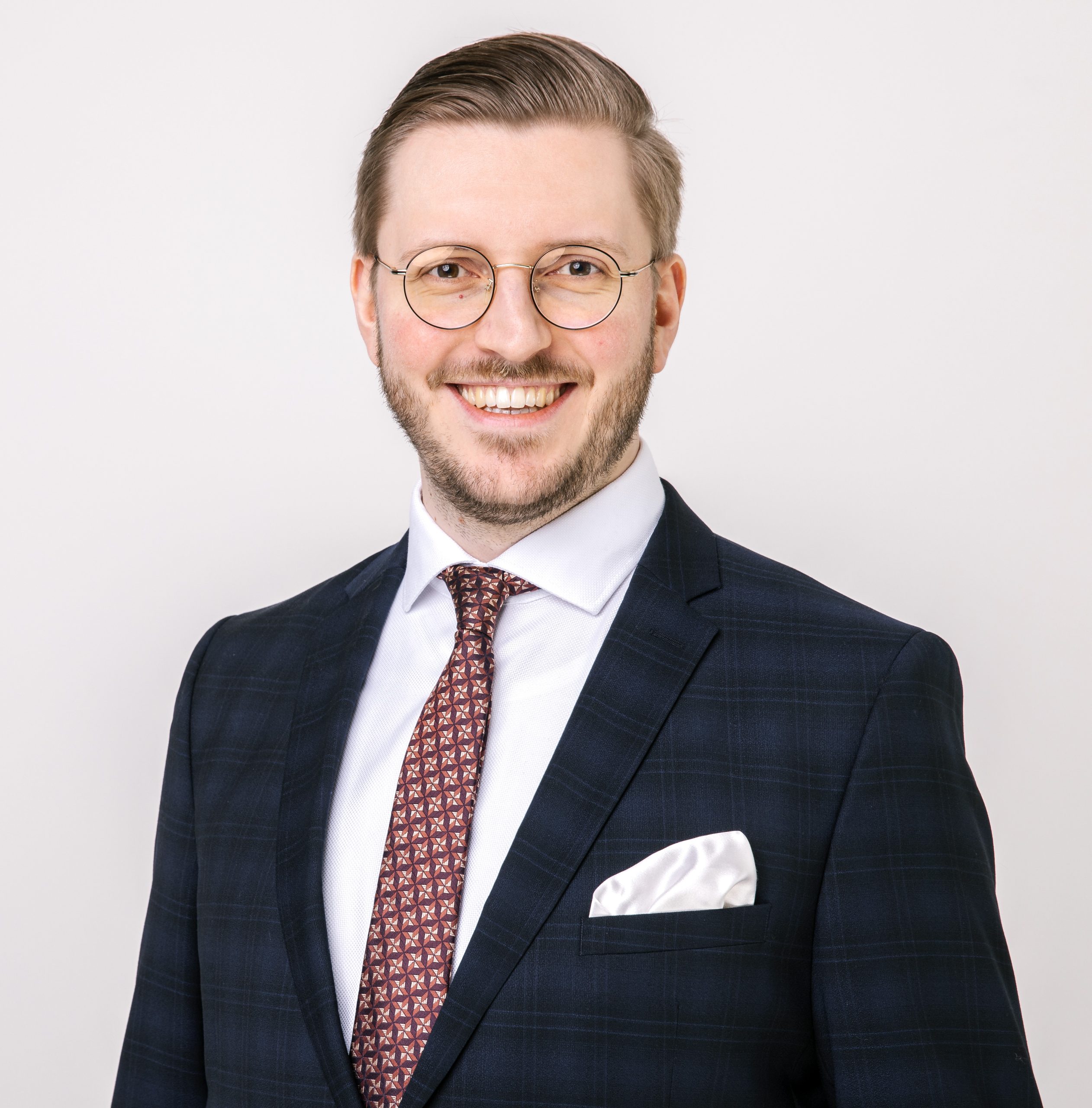
ALEXANDER SCHERER
Das könnte Sie auch interessieren:
So nutzen unsere Kunden Detact!