Intelligentes MES fürs Herz
KI-Upgrade für den Spritzguss
Endoskope, Implantate oder Herzschrittmacher: Die fortschreitende Miniaturisierung technischer Bauteile macht viele minimalinvasive Eingriffe überhaupt erst möglich. Selbst nach einer Herz-OP können manche Patienten schon nach wenigen Tagen wieder nach Hause. Ein typisches Beispiel für diese Entwicklung sind interkardiale Pumpensysteme. Die weltweit verbreiteten Medizingeräte halten kranke Herzen während minimalinvasiven Bypass-Operationen am Laufen. Scholz fertigt die notwendigerweise winzigen Komponenten für Herzpumpen an – jetzt auch mit den KI und MES funktionen von Detact.
High-Tech und Miniaturisierung
Analog zur Miniaturisierung steigt auch der Anspruch an die technischen Komponenten – selbst kleinste Abweichungen können die Funktion des gesamten Systems beinträchtigen oder ungewollte Verletzungen herbeiführen. Zulassungsbehörden wie die FDA oder Benannte Stellen erheben daher besonders strenge Vorgaben in Bezug auf Präzision sowie Zuverlässigkeit von Medizingeräten und seinen Bauteilen und fordern eine lückenlose Dokumentation des gesamten Herstellungsprozesses.
Dies gilt umso mehr, wenn ein komplexes Produkt aus zahlreichen Komponenten von verschiedenen Herstellern besteht – so, wie die meisten Herzpumpen – deren Erfolg in großen Teilen von der Präzision der einzelnen Bauteile getragen wird. Die dafür notwendigen, wenige Millimeter großen, komplex geformten Komponenten werden von Scholz HTIK aus Kronach im Mikrospritzguss gefertigt.
Daten, Daten, Daten
Der Außendurchmesser essenzieller Teile liegt oft unter einem halben Zentimeter, in der Qualitätssicherung braucht es daher eine genaue und stetige Überprüfung aller verfügbaren Mess- und Spritzgussparameter im Fertigungsprozess – um möglichen Veränderungen in Materialzusammensetzung, Verschleiß oder Temperatur durch feinjustierte Maschineneinstellungen ausschussfrei zu begegnen und eine zuverlässige Funktion der gesamten Herzpumpe zu garantieren.
Zusätzlich zu seinen erfahrenen Mitarbeitern erfasst Scholz HTIK wichtige Maschinendaten mithilfe eines MES Systems. Wirklich genutzt wurde das MES mit all seinen Informationen allerdings anfangs nur für das retrospektive Qualitätsmanagement oder die Fehlersuche bei sehr seltenen Reklamationen.
Mit einer zunehmenden Automatisierung der Kunststoffproduktion und dem rasant wachsenden Datenvolumen wuchs der Wunsch und die Notwendigkeit die Fertigungsdaten systematisch zu analysieren. Tammo Kemnitzer, Leiter des Technikums bei Scholz, ist u.a. für reibungslos funktionierende Fertigungsprozesse zuständig; er sagt: »Fast jedes Einzelsystem liefert eigene Daten und unsere Fertigung besteht aus zahlreichen Maschinen bzw. Anlagen. Dazu kommen die Daten aus unserem sehr engmaschigen Qualitätsmanagement. Irgendwann war die Datenmenge einfach zu groß. Wir konnten die wertvollen Informationen jedoch nicht ignorieren, sondern wollten sie zusammen mit anderen Parametern auswerten und visualisieren. Zudem war unsere Technik damals nicht Big-Data-fähig – wir mussten neue Wege finden, um einen echten Nutzen aus den Daten zu ziehen.
Das ‚alte‘ Erfolgsgeheimnis: Sehr viel Erfahrung
Tatsächlich fehlte den Mikrotechnik-Experten von Scholz – wie vielen anderen Herstellern auch – zunächst die richtige Technologie, um die enorme Datenflut mit einer einzigen Software sinnvoll darzustellen und zu nutzen – ohne Dateninseln und mit einem ganzheitlichen »Just in time«-Blick auf die Fertigung. Doch das bayerische Familienunternehmen hatte sich mittlerweile auch in der Medizintechnik einen erstklassigen Ruf erarbeitet, den es zu verteidigen galt. 2019 entschied sich Scholz für das Big-Data-fähige KI-System Detact. Die Software entsprach den vielfältigen Anforderungen an Flexibilität, Schnelligkeit und Vielfältigkeit und wurde mit der Zielsetzung angeschafft, Prozessveränderungen bereits im Vorfeld zu erkennen und für eine bestmögliche Qualität bei gleichzeitig geringem Ausschuss direkt reagieren zu können.
Der Fertigungsspezialist Kemnitzer sagt: »Eigentlich begannen unsere Herausforderungen schon bei der Aufzeichnung der Spritzgießparameter. Diese enormen Werte müssen einfach, visuell und vor allem schnell dargestellt werden. Nur so ist eine stabile Teilequalität aus dem Spritzguss auch bei wechselnden Bedingungen und unter natürlichen Schwankungen erreichbar. Für eine exzellente Qualität braucht es Fingerspitzengefühl, viel Erfahrung und eine hervorragende Messtechnik, um den Fertigungsprozess auch während der Produktion immer wieder anzupassen. Das KI-System Detact hilft uns, alle wichtigen Protokolle und Werte deutlich einfacher und schneller darzustellen.«
MES plus KI: Alles bleibt besser
Im Pilotprojekt für die Fertigung der Herzpumpen-Komponentensollte Detact die Daten aus dem Mikrospritzguss erfassen sowie systematisch analysieren. Die KI-Spezialisten des Herstellers Symate wurden beauftragt, zahlreiche Datenquellen anzubinden und das bereits vorhandene MES-System um die Detact-spezifischen Funktionen für die intelligente Datenerfassung bzw. -analyse zu erweitern. Scholz HTIK wollte das gesamte Parameterfeld mithilfe der Künstlichen Intelligenz überwachen lassen, um im Gegensatz zum bestehenden MES große Datenmengen zu verarbeiten und Abweichungen mithilfe der Kombinatorik zeitnah zu erkennen.
Um den Aufwand für die Einführung des neuen KI-Systems bei Scholz minimal zu halten, wurde Detact an die bestehenden Systeme angebunden, ohne diese grundsätzlich zu verändern. So konnten alle bisherigen Maschinen und Anlagen nahtlos weiterlaufen und selbst das bewährte MES blieb mehr oder weniger unangetastet. Lediglich für die Erfassung der bisher ungenutzten Daten wurden zusätzliche Schnittstellen eingerichtet.
Fakten statt Bauchgefühl
Das Ergebnis: Mit der Einführung des KI-Systems Detact hoben die Fertigungsplaner von Scholz HTIK ihre Datenerfassung innerhalb von wenigen Wochen auf ein völlig neues Niveau. So konnten sie die Qualität ihrer Bauteile nachhaltig sichern sowie die Aufbereitung relevanter Daten deutlich steigern – parallel dazu stieg die OEE (Overall Equipment Efficiency) in der Mikrospritzgussfertigung.
Dateninseln, ungenutzte Daten und langwierige manuelle Analysen gehören dazu der Vergangenheit an. Durch die prozessübergreifende Verarbeitung der ohnehin vorhandenen Prozess-, Qualitäts- und Umgebungsdaten als Gesamtpaket inklusive ihrer Analyse in einer zentralen Plattform erzeugt das lernende KI-System eine Transparenz, die mit herkömmlichen Technologien praktisch nicht erreichbar ist.
Diese Transparenz war das eigentliche Ziel der Mikrospritzguss-Spezialisten von Scholz HTIK. Nur so ist es möglich, Veränderungen in den Parameter und damit Prozessanpassungen systematisch vorher zu sagen – und die Qualität durch Feinjustierung konstant hoch zu halten. Kemnitzer erinnert sich noch gut an die Diskussionen mit seinen Kollegen: »Natürlich wollten wir auch bei der Herstellung der kleinen Herzpumpen-Komponenten beweisen, dass wir die Experten für absolute Präzision und Qualität sind – auch und gerade bei den winzigen, hoch anspruchsvollen Bauteilen. Zumal solch ein Medizingerät über Leben und Tod entscheidet. Viel Zeit und Kraft in unser Qualitätsmanagement zu stecken, war für uns schon immer selbstverständlich. Als wir zum ersten Mal von Detact hörten, wurden wir sofort neugierig, denn die KI-Experten von Symate haben weitreichende Erfahrungen mit derartigen Aufgaben. So schmiedeten wir sehr schnell konkrete Pläne für ein erstes Pilotprojekt und nur wenige Wochen später stellte das System auch schon die ersten Prozess-, Maschinen-, Qualitäts- und Umgebungsdaten unserer Herzpumpen-Komponenten visuell dar.«
Das Pilotprojekt wird erweitert
Kemnitzer ergänzt: »Mittlerweile haben wir sehr viel Erfahrung mit dem neuen KI-System und die Ergebnisse sprechen noch immer dieselbe Sprache: Wir verstehen mithilfe der ausgewerteten Daten die Fertigungsprozesse Millimeter großer, komplexer Bauteile exakt – in jedem einzelnen Moment. Dadurch haben wir alle Stellschrauben jederzeit unter Kontrolle. Genau das tun wir heute nicht anhand eines Bauchgefühls, sondern auf der Basis von objektiven Daten – und zwar ohne, dass uns die große Menge der Daten überfordern könnte. Im Gegenteil: Je mehr Daten wir heute verarbeiten, umso transparenter wird unser Gesamtprozess und desto zuverlässiger bzw. reproduzierbarer sind die Ergebnisse.«
Nach den Erfolgen des Pilotprojektes hat Scholz den Einsatz des neuen KI-Systems deutlich ausgebaut. Mittlerweile übernimmt Detact sogar die Aufgaben einer zentralen Infrastruktur für die Prozessbewertung und soll nach und nach den kompletten Anlagenpark bei Scholz HTIK auswerten. Dabei vergleicht die Software jeden einzelnen Auftrag mit einer Vielzahl von (externen) Bedingungen sowie den Daten aus parallellaufenden Prozessen. Auf dieser Basis lassen sich die Fertigungsprozesse nicht nur systematisch planen, sondern auch abbilden. Denn: Detact erstellt aus mehr als 300 Einzelparametern für jeden einzelnen Zyklus einen digitalen Datenfingerabdruck und somit die entscheidende Grundlage für die nachfolgende KI-Analyse. Dabei erfasst das intelligente System jede Abweichung vom Standardprozess und vergleicht wiederkehrende Muster anhand von speziellen Algorithmen. So erkennt die KI frühzeitig, wenn ein Prozess droht, aus dem vordefinierten Fenster zu laufen.
Zuverlässige Prozessfenster bis zum Rand des Machbaren
Für die umfassende Prozessbegleitung wird die KI zunächst trainiert und mit allen möglichen Rahmenbedingungen inklusive der entsprechenden Kennzahlen aus Prozess und Qualität etc. ‚gefüttert‘. Sobald das System die relevanten Parameterwechselwirkungen in mathematische Modelle übertragen und validiert hat, kann der Prozess ohne Unterbrechung starten. Das KI-System wertet die anfallenden Prozess- und Qualitätsdaten dann im Sinne einer Gesamtparameterbetrachtung statistisch aus und stellt die Ergebnisse in grafischen Tabellen, Diagrammen oder Punktwolken dar.
Mit der ganzheitlichen Prozessvalidierung im Rahmen der laufenden Produktion ist es heute bereits möglich, Prozesse in einem sehr engen Toleranzbereich zuverlässig zu ‚fahren‘ – bei Bedarf sogar bis an die Grenze des technisch Möglichen. So bleibt genügend Zeit für Vorbereitung und Reaktion, ohne die Qualität der Bauteile zu gefährden. Zudem unterstützt Detact die aufwändigen fertigungsbegleitenden Prüfungen und spart viel Zeit.
Qualität UND Effizienz
Auch wenn das neue KI-System vor allem zur Sicherung der Bauteilqualität angeschafft wurde, schauen die Verantwortlichen bei Scholz auch sehr genau auf die Effizienz ihrer Prozesse. Die Investition in das KI-System muss sich rechnen. Da vor allem Stillstandzeiten zu erheblichen Kosten und Verzögerungen führen, haben sie die Verfügbarkeit und Auslastung ihrer Maschinen ebenso fest im Blick. Zukünftig möchte Scholz HTIK die von Detact gewonnen Informationen zusätzlich für eine vorbeugende Wartung nutzen, welche die Basis für Predictive Maintenance legen soll. Die klassische Wartung ist fast immer aufwändig und teuer, denn sie muss regelmäßig erfolgen. Erst dann lassen sich unplanmäßige Ausfallzeiten überhaupt vermeiden. Mit dem digitalen Datenfingerabdruck von Detact sollen die engmaschigen klassischen Wartungen der Vergangenheit angehören. Statt vorbeugend zu agieren, können Wartungen anhand des prognostizierten Maschinenzustandes geplant werden, wenn sie aufgrund der Wahrscheinlichkeit von potenziellen Drifts wirklich erforderlich sind. Das reduziert Materialeinsatz und Stillstandszeiten.
Bei Scholz HTIK soll das Detact-Tool zu einer Infrastruktur für den Einsatz von Künstlicher Intelligenz in der Qualitätssicherung werden und zu einem Basis-Werkzeug für die autonome Fertigung der Zukunft.
»Detact hat unsere Fertigungsprozesse wesentlich transparenter gemacht. Gleichzeitig sind sie auch effizienter geworden. Diesen Trend konnten wir schon bei unserem Pilotprojekt feststellen. Die Software hat uns in Sekundenschnelle alle relevanten Daten dargestellt. Das KI-System entlastet damit unsere Abteilungsleiter, die diese Analysen bisher separat und mit hohem Zeitaufwand erstellten. Zudem konnten wir den Produktionsablauf im Mikrospritzguss deutlich verbessern. Diese Ergebnisse sind weit mehr, als wir erwartet hatten – und dennoch erst der Anfang.«
Das KI System Detact
Das Tool Detact ‚KI-Infrastruktur & Apps‘ sammelt, analysiert und verarbeitet Maschinen-, Qualitäts- und/oder Umgebungsdaten. Das Softwaresystem wurde an der Technischen Universität Dresden entwickelt und arbeitet mit nahezu allen Datenquellen bzw. Schnittstellen und nutzt Methoden der Künstlichen Intelligenz. Es bietet flexible Funktionalitäten für eine automatisierte Prozessüberwachung sowie nachhaltige Prozesstransparenz. Dabei übernimmt Detact auch die meisten Aufgaben eines klassischen MES (Manufacturing Execution System), geht aber weit darüber hinaus.
Über die Symate GmbH
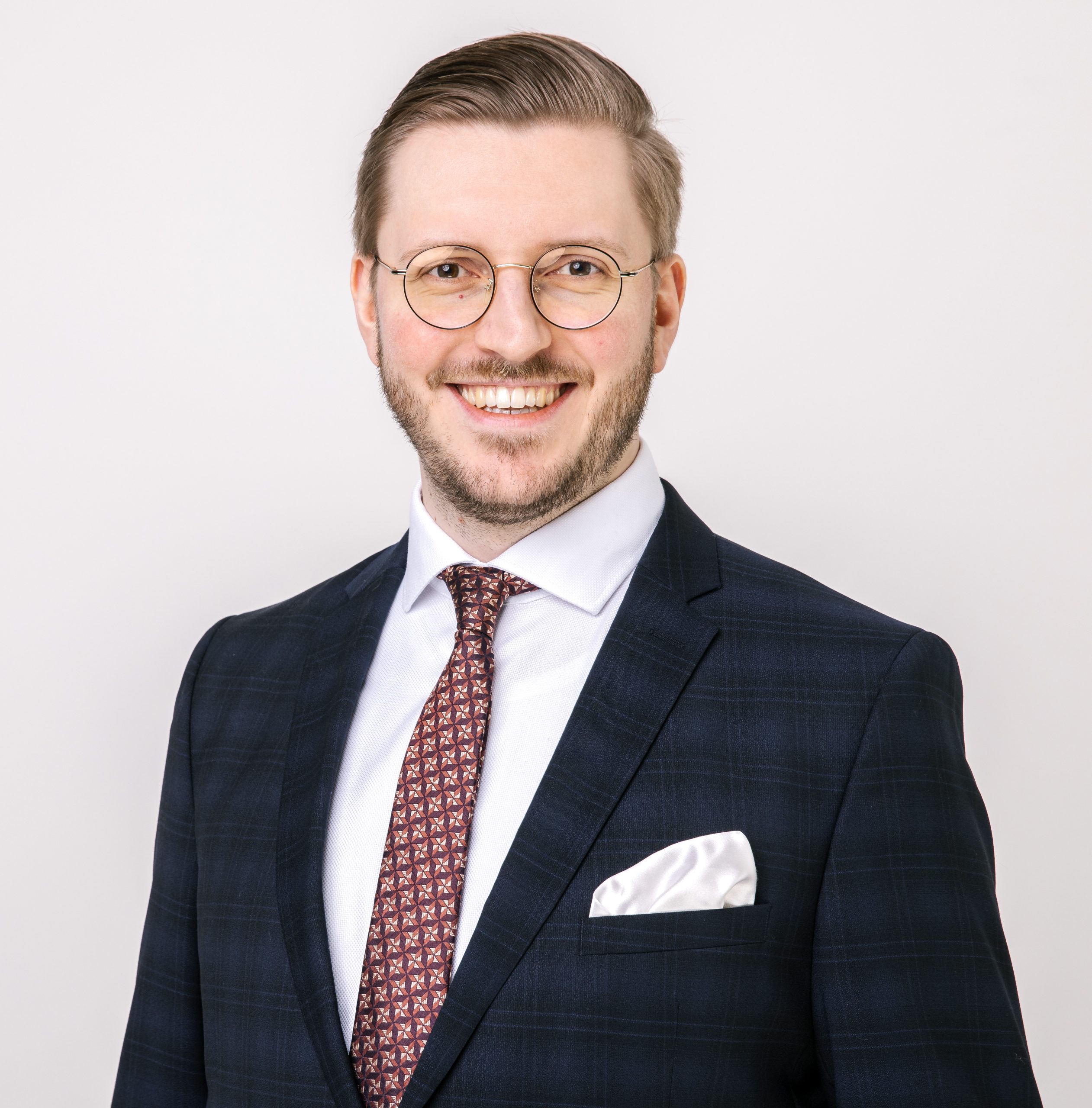
ALEXANDER SCHERER
Das könnte Sie auch interessieren:
So nutzen unsere Kunden Detact!