Optipack setzt auf MES-System, KI und Maschinendatenerfassung für optimierte Prozesse
Quality Prediction in der Verpackungsindustrie mit Detact
Die Optipack GmbH der Unternehmensgruppe Theo Müller und Symate implementieren die Qualitätsprognose in Thermoforming-Prozessketten mit Detact.
Detact ist das umfangreichste KI-Dashboard zur Digitalisierung und Optimierung von Fertigungsprozessen. Detact erfasst alle relevanten Daten komplexer Prozessketten und verarbeitet diese in maßgeschneiderten Analyse- und KI-Apps (Künstliche Intelligenz) für Ingenieure und Anlagenführer.
Die Optipack GmbH ist Hersteller von PS-, PP- und PET Verpackungen und einer der wichtigsten Zulieferunternehmen der Nahrungs- und Genussmittelindustrie. In Leppersdorf sind dazu modernste Extrusions- und Tiefziehanlagen im Einsatz, denen Kunststoffbecher und PET Preforms für die Lebensmittelindustrie FMCG (fast moving consumer goods) gefertigt werden.
Da strenge Vorgaben an die Maßhaltigkeit, Geometrie sowie Oberflächengüte der Becher eingehalten werden müssen, gibt es aufseiten der Qualität wenige Spielräume. Vor dem Hintergrund einer Soll-Ausbringungsmenge von ca. 2,5 Mrd. Einheiten pro Jahr ist die Absicherung der Prozesstabilität eine der wesentlichen Zielgrößen für den Standort, um eine wirtschaftliche Produktion zu gewährleisten.
Erwartungen von Optipack und erste Schritte zur Implementierung von Detact
„Wir erwarten uns von Detact ein Mehr an Unterstützung und Automatisierung bei der Prozessführung insb. im PP- und PSBereich. Unsere Fachkräfte sind stark eingebunden in neue Projekte. Umso wichtiger ist es, mit Detact den Herstellungsprozess weiter zu optimieren um somit Freiräume für wei – tere Aufgaben/Entwicklungen zu schaffen.“, berichtet Thomas Böhme, Entwicklungsleiter bei Optipack. Im ersten Schritt wird Detact dazu an einer ausgewählten Tiefziehanlage eingerichtet. Dies umfasst
Ein Datenquellen-Set-Up in Detact mit allen technologisch relevanten Datenquellen (z. B. für das vorhandene BDE-System Aspen InfoPlus.21 und für Qualitätsmesswerte in Excel-Dateitypen sowie Klimawerte als CSV-Dateien). Vorkonfigurierte Verarbeitungs-Pipelines sind von Symate einzurichten, um eine Direktanbindung der Einzeldatenquelle in Detact zu ermöglichen und die übergreifende Zusammenführung der Rohdaten zu einer Gesamtparameterbetrachtung für Dosieren, Extrusion und Tiefziehen mit Qualitätsdaten wie Durchmesser Siegelrand, Stauchdruck, Wandverteilung etc. und Gebäude- und Klimadaten permanent zu realisieren.
Ein App-Set-Up in Detact. Nach der LiveSchaltung der Datenquellen findet die Einrichtung von Analyse und KI-Apps in Detact statt. Ziel ist es die permanent anfallenden Unmengen an Rohdaten aus allen Elementen der Prozesskette automatisch zu analysieren und Auffälligkeiten im Prozesszustand zu finden.
Erläuterung der Ziele und Prozesse von Symate und Optipack
„Es geht uns darum, mit Detact ein Prozessketten übergreifendes Gesamtbild aller relevanter Parameter von Material- und Umgebungsbedingungen, von Werkzeugkühlung, Prozessabläufen, unterschiedliche Einstellstrategien der Maschinenführer bis hin zum Komponentenverschleiß aufzubauen. Zwar verhält sich der Tiefziehprozess relativ stabil; allerdings in einem engem Prozessfenster. Wir wollen Einflüsse auf die Prozessstabilität und / oder Qualitätsmerkmale mit Detact sichtbar machen; insgesamt den Prozess für Optipack besser kontrollierbar machen.“, erläutert Dr. Martin Juhrisch, Geschäftsführer der Symate GmbH.
Schon vor der gemeinsamen Zusammenarbeit wurden permanent große Datenmengen an den Tiefziehprozessketten aufgezeichnet; aber nur ein abgegrenzter Teil operativ genutzt. Daten wurden nur in Problemsituationen gesichtet. Mit den bisherigen Möglichkeiten war es auch nahezu unmöglich, Parametereinflüsse und Interaktionseffekte zwischen diversen Parametern zu beschreiben. Genau das ist aber zukünftig gewünscht, um den Prozess noch sicherer und robuster zu machen.
Verwendung von KI-Apps und Datenanalyse zur Optimierung
Symate als Hersteller von Detact konzentrierte sich deshalb von Anfang an auf die Bereitstellung von zwei KI-Apps: die Detact Quality Prediction App für die Validierung des aktuellen Prozesszustands in Hinblick auf Bauteilqualitäten auf Basis der kontinuierlichen Berechnung einer Fehlerwahrscheinlichkeit und die Detact Recommendation App für die Visualisierung von Handlungsempfehlungen für eine Optimierung der Prozesskette bei Prozess- und Qualitätsschwankungen. Ziel ist es die Entwicklung kritischer Qualitätsparametern wie Maßhaltigkeiten und Oberflächenbeschaffenheit im laufenden Prozess zu prognostizieren. Zudem soll eine Mustererkennung gute und weniger optimale Prozessfenster markieren und Handlungsempfehlungen für Maschinenführer geben.
Vor der eigentlichen Automatisierung wurde ein Parameterscreening auf Basis von Datenexploration, Feature Engineering und Modellbildung über Parameterwechselwirkungen durchgeführt. Bestandteil waren der Einsatz von lernfähigen mathematischen Methoden (u. a. Decision Trees und Neuronale Netze) und die Analyse von Auswirkungen von Parametervariation und Modellbildung über Parameterwechselwirkungen. In Zusammenarbeit mit Optipack wurden die identifizierten Zusammenhänge zwischen Ziel-, Einfluss- und Störgrößen visualisiert und nach den entscheidenden qualitätsrelevanten Parametern priorisiert.
Ergebnisse und Auswirkungen der Implementierung von Detact
Die Ergebnisse der Modellbildung zeigen eine gute bis sehr gute Vorhersagegenauigkeit von NIO-Teilen; d. h. NIO-Teile im Prozess, ohne das real gemessen wurde, die je nach Lernphase für die Algorithmen zwischen 3 und 25 % Abweichung vom Realwert beträgt. „Dies bedeutet für uns die frühzeitige Kenntnis über Qualitätsabweichungen in der Fertigung und Wegfall von unnötigen Prüfungen und Entlastung der Qualitätssicherung. Wir gehen von einer potentiellen Reduzierung der Auslastung der Qualitätsüberwachung aus.“, sagt Thomas Böhme.
Die Detact Recommendation App wiederum gibt dem Anwender Informationen darüber, wie sich der Prozess um das aktuelle Prozessfenster herum verhält und wie er durch die Veränderung einzelner oder mehrerer Parameter auf in andere Zustände geführt werden kann. Mit jedem weiteren erkannten Muster wird das Technologie-Know-how gewissermaßen iterativ validiert und erweitert, was zu einer wirtschaftlicheren Prozessführung führt. „Wir versprechen uns davon eine Erhöhung der Robustheit im Prozess und ein schnelleres Zurückführen in einen stabilen Zustand nach Ausbrechen.“ so Böhme.
Was zunächst nach viel zusätzlichem Aufwand klingt, wird größtenteils durch Detact erledigt. „Durch eine Kombination aus fertigen Elementen und anpassbaren flexiblen Elementen in Detact kann eine produktive Lösung beim Kunden sehr schnell bereitgestellt werden, da standardisierte Elemente wiederverwendet werden können. Die flexiblen Elemente in Detact lassen sich auf die individuellen Anforderungen des Kunden hin anpassen. Die Einrichtung hat pro App nimmt ca. 10 Manntage in Anspruch“, kommentiert Dr. Martin Juhrisch, Geschäftsführer der Symate GmbH den Aufwand.
Ausblick und zukünftige Entwicklungen
„Aktuell stehen wir vor der eigentlichen Automatisierung der beiden Apps, damit diese durch Maschinenbediener direkt bedient werden können.“
Die Entwicklung der Algorithmen findet auf Basis von Cluster Computing im Detact Data Center statt. Dies erlaubt ein Maximum an Verarbeitungsgeschwindigkeit durch eine skalierbare Architektur, die durch eine Parallelisierung der Datenverarbeitung und Datenspeicherung gekennzeichnet ist. Die Technologie ermöglicht komplexe Analysen auf großen Datenmengen in Maschinennähe durchzuführen. Im Detact Cluster werden sukzessiv beide Apps freischalten. Die Anwender können dann über Browser oder Tablet noch intensiver unterstützt werden. Dies ist ein wichtiger Schritt zu einer autonomeren, selbstregelnden Prozessführung, ist sich Dr. Juhrisch sicher
„Derartige Digitalisierungsprojekte sind für unsere Kunden eine große Herausforderung. Deshalb ist es umso wichtiger, dass Detact ein schrittweise Einsteigen mit Datenquellen ermöglicht, die ohnehin bereits Technologiedaten enthalten. Dadurch entstehen Lösungen, die auf heterogene Prozessketten passen, in kurzer Zeit bereitgestellt werden können und wirklich weiterhelfen.“
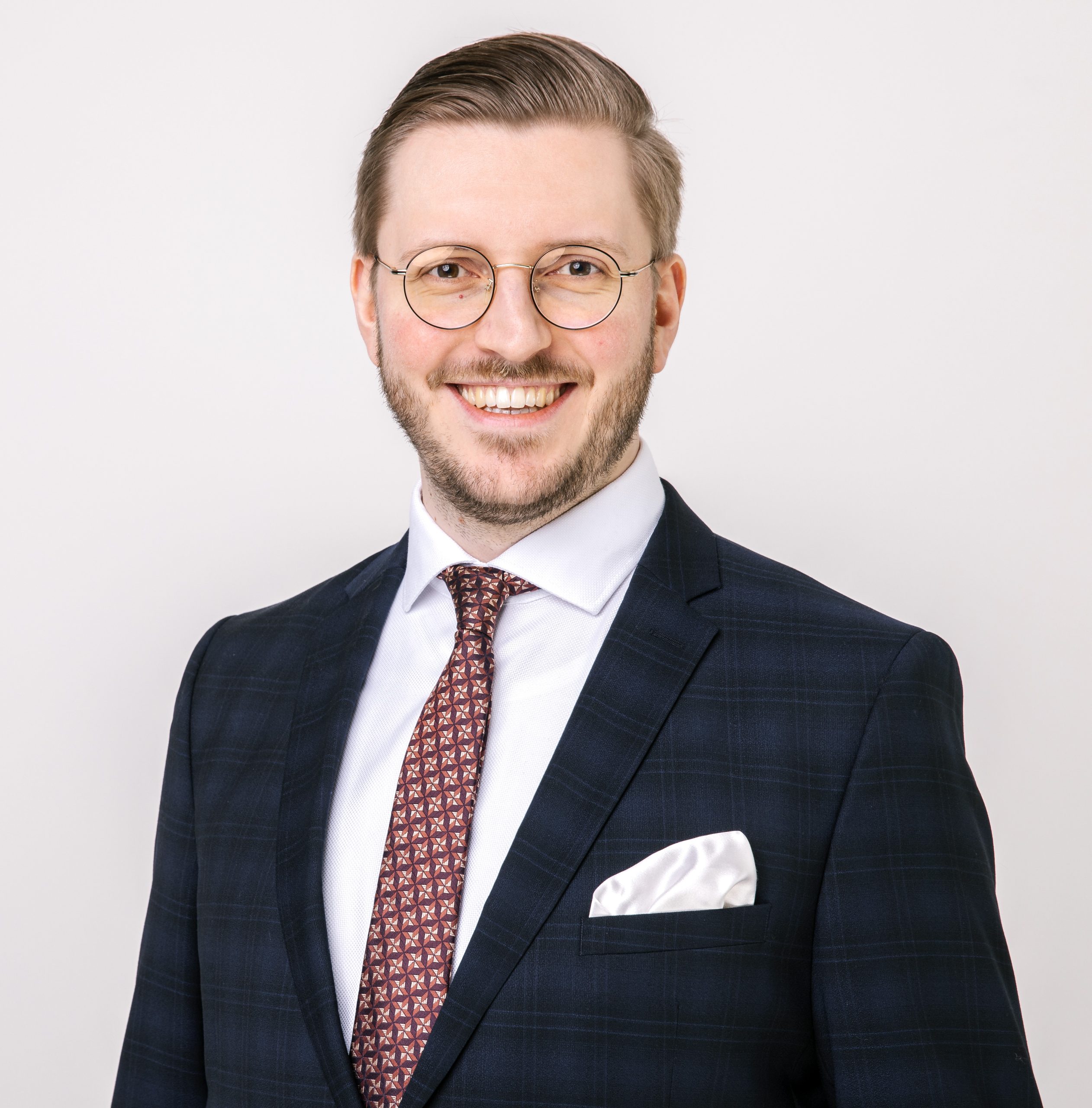
ALEXANDER SCHERER
Das könnte Sie auch interessieren:
So nutzen unsere Kunden Detact!